Heavy Duty Side Entry Agitators
Types: RWM
Blending (petro)chemical products, paper & pulp are examples of heavy duty applications where side entry agitators and mixers are selected.
Characteristics for heavy duty agitators and mixers are:
- Mixing applications where extremely high forces are required
- Very large tank volumes (multiple mixers in one tank possible)
- Fluids are highly viscous exceeding even 75.000 cP
- Pressure tanks exceeding even 5 bar
- Temperatures exceeding 250 °C
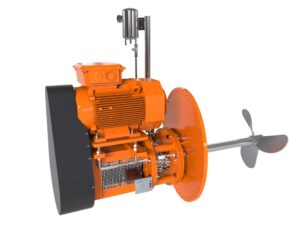
Heavy Duty Side Entry | |
---|---|
Motor power | 11 kW – 55 kW |
Materials | Stainless Steel 304, 316 L, Carbon Steel, Duplex (Super), Hastelloy C4 or C2000, Titanium Grade 2 or 7 |
Coatings | C3, C4, C5 of C5M |
Surface wetted parts | Ground until Ra < 0,4 µm, handpolished till <0,2 μm or electropolished, rubber lined, PTFE or HALAR |
Explosion proof (ATEX) | Ex zone 0, 1 or 2 for gas, 21 or 22 for dust or Non-Ex version |
Accessories | V-belt or gear driven (all brands), all kinds of sealing systems, sterile versions, adapted flanges to vessel |
RWM mixers
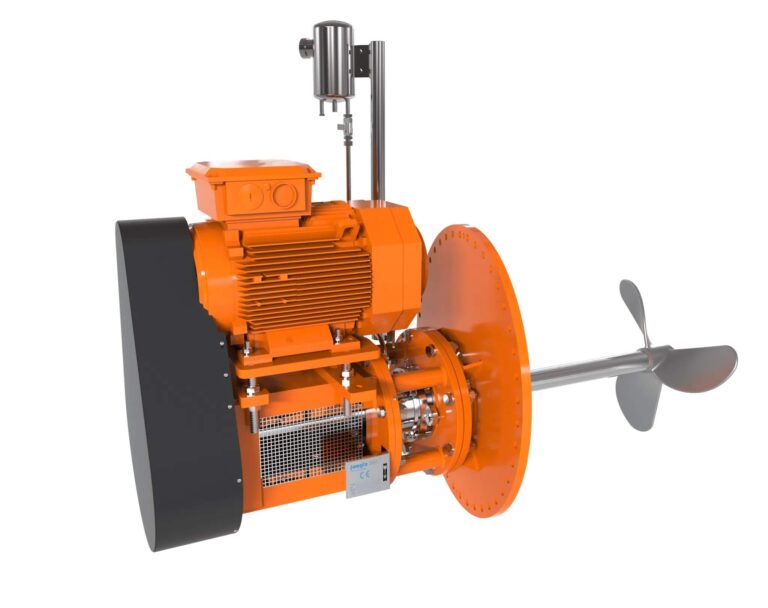
Jongia’s mixer type RWM is a side entry mixer that is suitable for heavy duty operation. A few specifications of the RWM side entry mixer:
The mixer shaft has a separate bearing.
The shaft is coupled to the drive by means of a belt type transmission.
The mixer is equipped with an outside single or double mechanical seal.
An optional design allows the exchange of seals while the tank is completely filled. In this configuration it is especially suitable in large storage tanks. Besides, a heavy petrochemical industry construction in accordance with API (American Petroleum Institute) is available.
Applications Heavy Duty Side Entry Agitator – RWM
Frequently Asked Questions
What types of applications are suitable for Heavy Duty Side Entry Agitators?
Heavy Duty Side Entry Agitators are ideal for applications requiring high mixing forces, large tank volumes, and the ability to handle very viscous fluids. They effectively blend petrochemical products, as well as paper and pulp, in demanding environments.
What are the motor power options available for RWM mixers?
RWM mixers offer motor power options ranging from 11 kW to 55 kW. This flexibility allows them to be adapted for various heavy-duty mixing applications, ensuring optimal performance for specific operational needs.
What materials are used in the construction of Heavy Duty Side Entry Agitators?
These agitators can be made from a variety of materials, including Stainless Steel 304, 316 L, Carbon Steel, Duplex, and specialized alloys like Hastelloy and Titanium. This variety ensures durability and resistance to harsh conditions.
Are RWM mixers designed for high-pressure and high-temperature applications?
Yes, RWM mixers are designed to operate in pressure tanks exceeding 5 bar and temperatures beyond 250 °C. This makes them suitable for various heavy-duty mixing tasks in extreme industrial environments.
What kind of sealing systems do RWM mixers have?
RWM mixers are equipped with outside mechanical seals, available in single or double configurations. An optional design allows for seal exchange even when the tank is filled, making them particularly useful in large storage tanks.
Contact our specialized team for all your questions
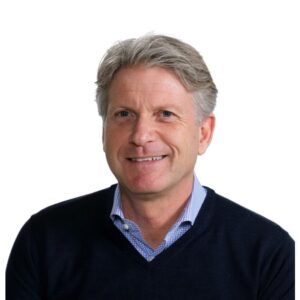
Tom Pruymboom
Sales Director
Area Worldwide
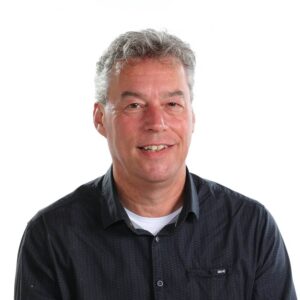
Bart Brouwer
Area Sales Manager
Area Worldwide
Related Articles
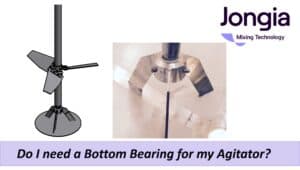
Do I need a Bottom Bearing for my agitator?
Do I need a Bottom Bearing? The installation of a bottom bearing is not mandatory. While it offers certain advantages, there are also drawbacks to consider. It is important to note that the bottom bearing functions more as a displacement
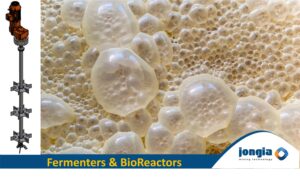
Fermentation & Bioreactor Mixing Process
Bioreactors and Fermenters are culture systems to produce cells or organisms. They are used in various applications, including basic research and development, and the manufacturing of biopharmaceuticals, food and food additives, chemicals, and other products. A broad range of cell types and organisms can be cultivated in bioreactors and Fermenters, including cells (like mammalian cell lines, insect cells, and stem cells), microorganisms (like bacteria, yeasts, and fungi), as well as plant cells and algae. The words “Bioreactor” and “Fermenter” are basically the same thing.
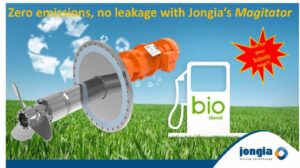
Biodiesel blending with zero leakage!
Fuel blending is a critical component of biodiesel production. A properly blended fuel can increase energy efficiency, reduce emissions and improve performance. However, it can be difficult to achieve consistent fuel quality during blending due to differences in storage tanks,