Gas Inducing Mixer
PROCESS:
Gas/liquid reactions with pure gases
TYPE OF PRODUCT:
Hydrogenated fatty acids – pharmaceuticals – hydrometallurgical products
APPLICATIONS:
Hydrogenation – Chlorination – Oxidation – Acylation – Alkoxylation – Amination – Carboxylation
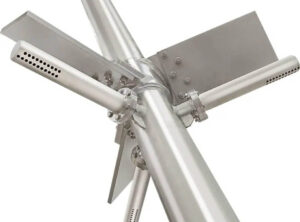
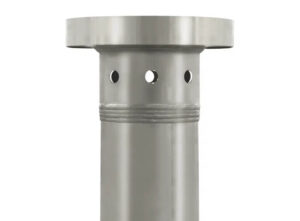
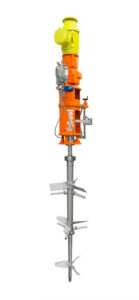
Gas Inducing Mixer for Food & Chemical industry
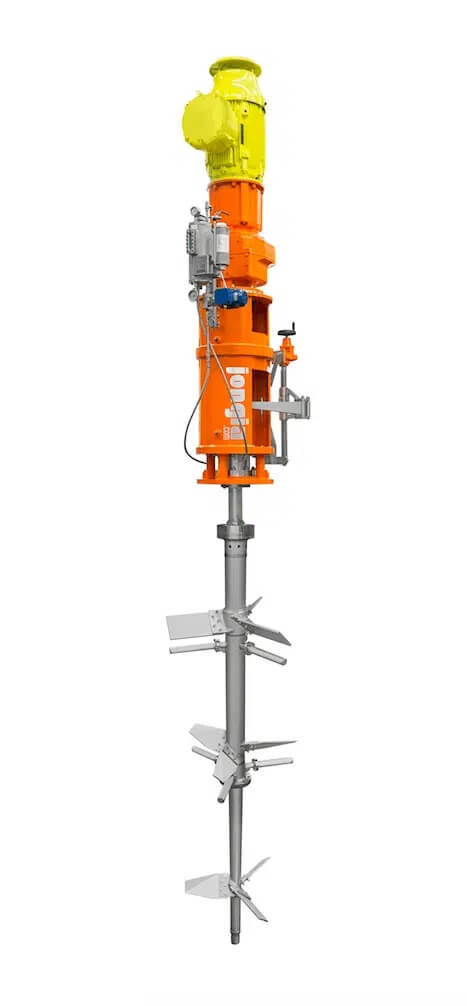
Jongia meets the challenge of modern-day high productivity requirements with its novel gas-inducing system. In a reactor a gas-inducing coil, the so-called sparger, is installed for the primary gas supply. The unused gas is collected in the head space of the reactor above the liquid level. This gas is recirculated through the hollow shaft and re-induced through the gas inductors mounted below the liquid level.
The main mixing element creates an under-pressure at the gas inductors to disperse the gas into the reaction media. Depending on the batch sizes required one or more combinations of mixing elements and gas inductors can be installed.
Thanks to recirculation of unconverted gas in the headspace of the reactor complete utilization of the reaction gas is achieved without the need for an external compressor. Jongia’s self-inducing mixer ensures high operating safety and reliability as the gas and catalysts are contained within the reactor. Instrumentation and control costs are limited and productivity is boosted thanks to high mass transfer rates as shown in the kLa values. The JONGIA design concept permits a low agitator speed so that the agitator-inducer system is operated below its critical speed and irregular loads on the shaft and bearings are avoided.
In short Jongia’s gas-inducing mixer combines:
- A high induced gas flow rate
- A fine dispersion of the gas and therefore a large interfacial area
- Accurately predicted excellent mass transfer also on large scale
- Stable mechanical operation at moderate (sub-critical) stirrer speed
- Recirculation of the unused gas
Applications
Gas Inducing Mixer Articles
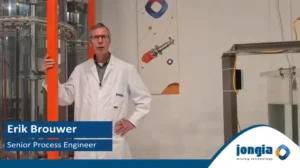
Tutorial: How does the Gas Inducing Mixer work?
Jongia Mixing Technology designed the Gas Inducing Mixer to dissolve gas in liquid in order to achieve a (chemical/biochemical) reaction. The mixer is most commonly used in hydrogenation (curing) processes and especially for hydrogenation of fats (acids) in the food

The Gas Inducing Mixer: from request to solution
When gas/liquid reactions with pure gases have to be created, the Gas Inducing Mixer is used. However, what type of customer comes to Jongia Mixing Technology for this agitator? And what are the next steps? What solution does Jongia Mixing
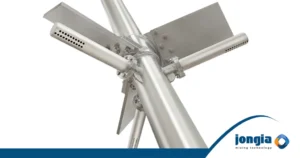
Gas Inducing Mixer: an unique design
Dissolving gas in liquid is not an easy task. This is exactly the reason why Jongia Mixing Technology developed its own Gas Inducing Mixer. The mixer is designed to make a gas/liquid dispersion. This means dissolving the gas in a
Frequently Asked Questions
What is the main function of the Gas Inducing Mixer?
The Gas Inducing Mixer is designed to facilitate gas/liquid reactions using pure gases. It effectively disperses gases into liquid media to enhance mass transfer rates during various chemical processes.
What types of products can be produced using the Gas Inducing Mixer?
The mixer can be used to produce hydrogenated fatty acids, pharmaceuticals, and hydrometallurgical products. Its versatility makes it suitable for a range of applications in these industries.
What chemical applications can the Gas Inducing Mixer accommodate?
The mixer is applicable for hydrogenation, chlorination, oxidation, acylation, alkoxylation, amination, and carboxylation. These processes benefit from the efficient gas induction provided by the mixer.
How does the Gas Inducing Mixer enhance productivity?
The mixer boasts high mass transfer rates, achieved through the recirculation of unused gases, eliminating the need for an external compressor, and operating at low agitator speeds. This results in stable operation and enhanced efficiency.
What are the benefits of using a recirculation system in the mixer?
The recirculation of unused gas ensures complete utilization of the reaction gas, thereby improving reaction efficiency. Additionally, it allows for high operational safety and reduced control costs due to contained gases and catalysts within the reactor.
Contact our specialized team for all your questions
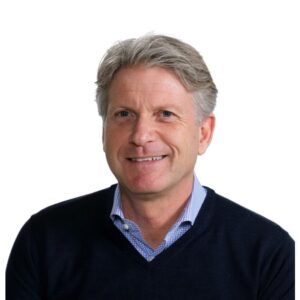
Tom Pruymboom
Sales Director
Area Worldwide
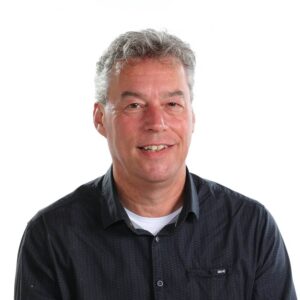
Bart Brouwer
Area Sales Manager
Area Worldwide
Technical Questions?
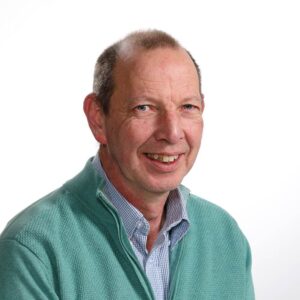