After Sales
Flexible and multifunctional
Process installations are often in continuous operation and are used to produce a wider variety of products. Therefore, new mixing equipment must be multifunctional and is subject to more demanding requirements. Guarantee/warranty conditions are also becoming increasingly strict. How does Jongia meet those (changing) requirements? Jongia offers the type of high-quality service that customers ask for with regard to Total Cost of Ownership (TCO) and Total Productive Maintenance (TPM) strategies. Service and maintenance are an integrated part of our stirring and mixing concepts. We have experienced and qualified service engineers available and guarantee swift reaction times.
Service contracts
Our service contracts are tailor-made to meet the requirements for preventive maintenance of your mixers. Our expert engineers will analyze your specific needs and offer you a maintenance plan as well as training services to instruct your personnel on maintenance and how to obtain maximum effectiveness from your mixers.
Frequently Asked Questions
What types of services does Jongia offer after installation?
Jongia provides various services including maintenance, spare parts supply, rental units, and process optimization. Our services ensure the longevity and efficiency of your mixing equipment, addressing any issues that may arise and improving overall performance.
How can I customize my maintenance plan?
Jongia offers tailor-made service contracts that are designed to meet your specific preventive maintenance requirements. Their expert engineers will analyze your needs and create a personalized plan that includes training for your personnel on proper maintenance practices.
Are spare parts readily available?
Yes, Jongia has spare parts often available from stock, machined in-house or sourced from reputable sub-suppliers. Our dedicated spares sales engineers are prepared to provide quick assistance to ensure minimal downtime for your equipment.
What support is offered during installation?
Jongia provides worldwide support during the installation and commissioning of your production equipment. Our experts ensure proper installation and functioning, which helps achieve optimal process results and enhances equipment durability.
How can I access 24/7 service?
Jongia has a global service network in collaboration with the HEINKEL Drying and Separation Group, ensuring 24/7 service availability. Our technicians are ready to help resolve issues quickly, reducing downtime and keeping your production running smoothly.
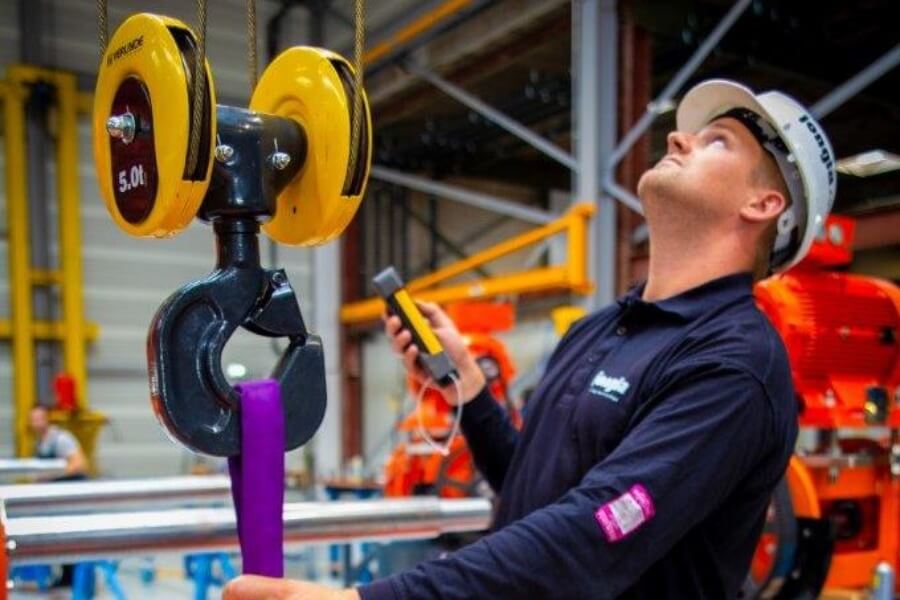
Maintenance
An agitator is the heart of your installation and should be running smoothly at all times. Our specialists will carry out the prescribed maintenance and ensure safe and durable operation providing you with continuity of production.
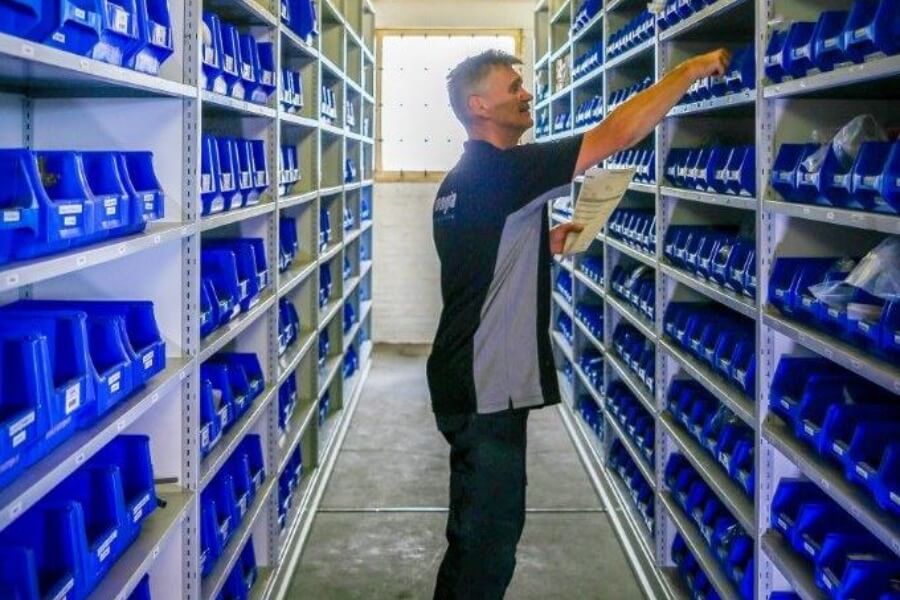
Spare Parts & Repairs
Spares machined in-house by our experienced operators or from well-reputed sub-suppliers are often available from stock or with the shortest possible delivery times. Our dedicated spares sales engineers are ready to assist you.
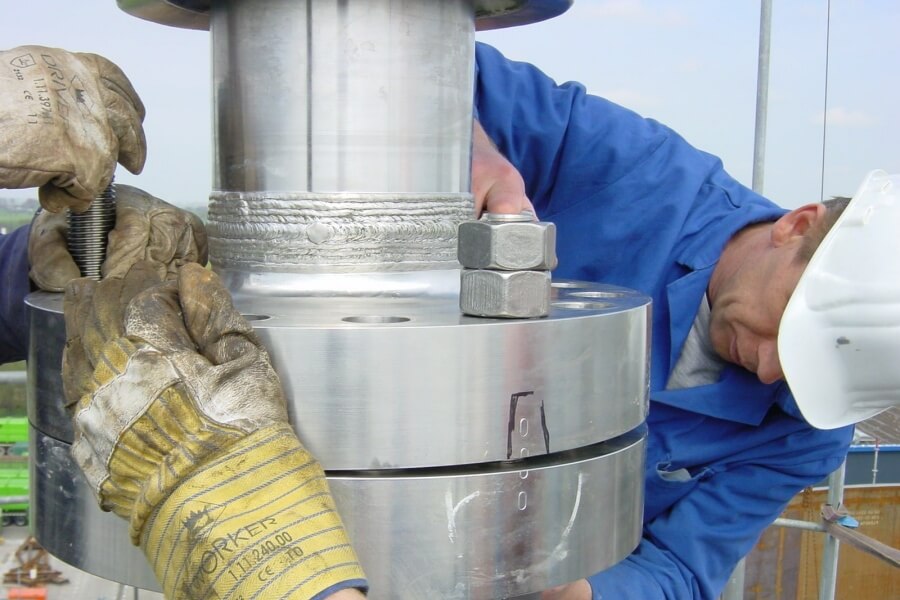
Installation & Commissioning
Our experts support you worldwide during installation and commissioning of your production equipment. Our support ensures proper installation and functioning of our equipment guaranteeing optimal process results and durability.
Download our VCA certificate here.
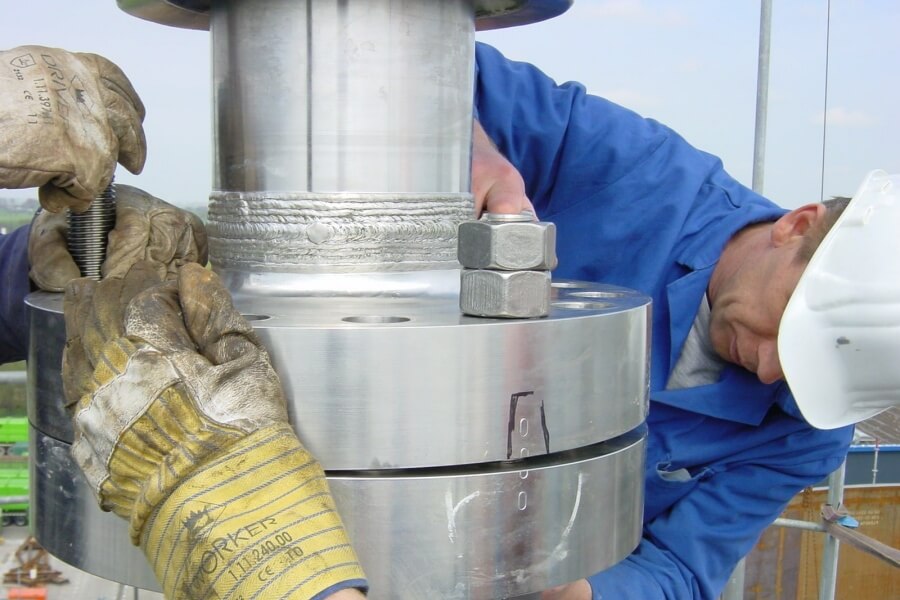
Service 24/7
Our worldwide service network, in cooperation with the HEINKEL Drying and Separation Group, is available to you 24/7. Our technicians help you solve problems fast and efficiently, so that your production can be up and running again quickly.
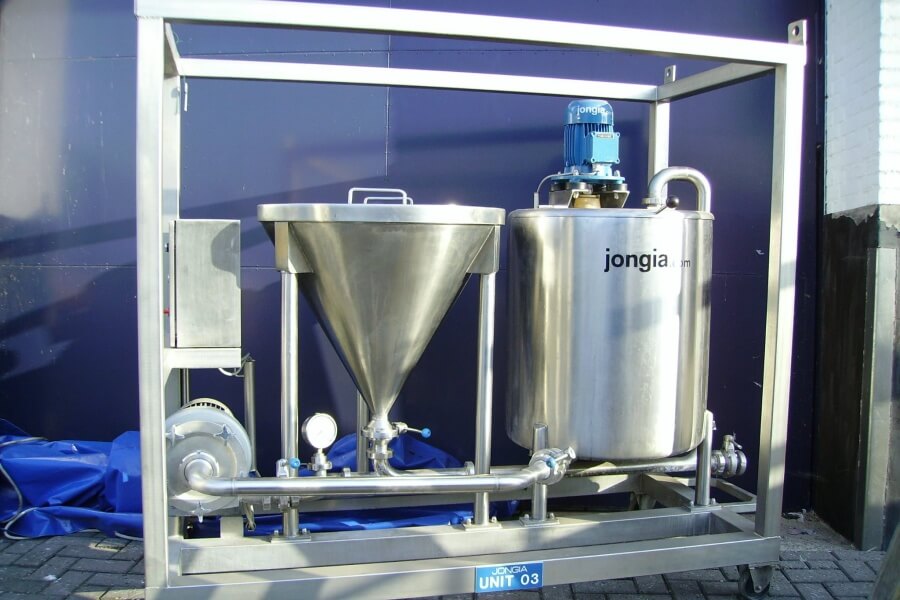
Rental units
We offer a rental equipment programme which enables process engineers to optimize a process before committing to a large capital purchase. Our process engineers are available to support you during testing with their expert advice.
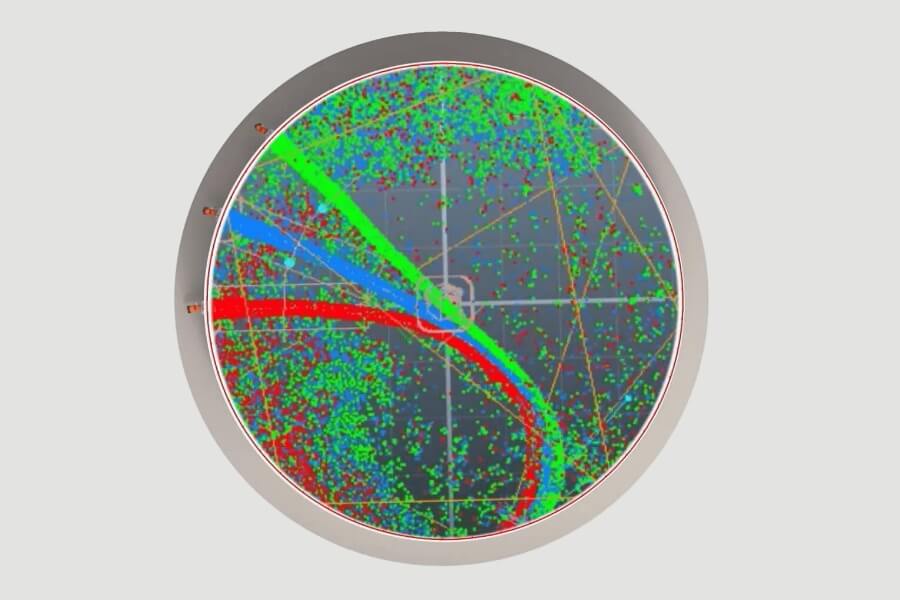
Process Optimisation
After commissioning, we will support you in the optimization of your process making sure our equipment functions to your satisfaction. Extensive tests provide information on the functionality and efficiency of the agitators in your production process.
We assist you during from inquiry to installation & commissioning and provide 24/7 after-sales services
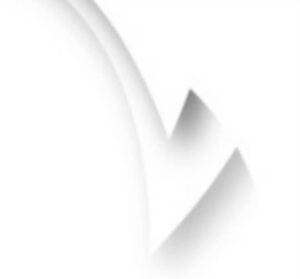
Stay informed
Sign up for our newsletter and receive the latest news
After Sales Posts
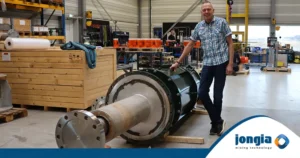
The introduction of: Service Aftersales employee Frank van den Hoed
Jongia Mixing Technology holds a good many professionals to its name. Every four weeks, we will introduce one of those professionals to you. This week, we’d like to introduce the 65-year-old Amsterdam-born Frank van den Hoed. Frank has been working
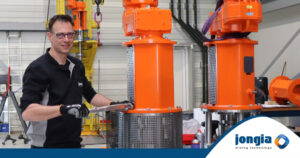
The introduction of: Manager Service After Sales Thonnis de Jonge
Jongia Mixing Technology holds a good many professionals to its name. Every four weeks, we will introduce one of those professionals to you. This week, the honors go to Thonnis de Jonge. He made his start in 1999 as Service
Other Recent Posts
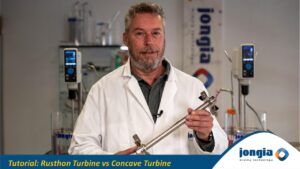
Tutorial: Rushton Turbine vs Concave Turbine
We are happy to announce on behalf of Jongia Mixing Technology that we have just launched a new tutorial on our website! This time, we take you into the world of mixing technology with an in-depth comparison between the “Rusthon

Mixing the correct Ion-Lithium Battery Slurry is a real challenge!
Lithium-based battery technologies for electric vehicles use lithium-ions as the charge carrier. Depending on the application’s technical requirements, lithium is used with various chemistries such as graphite for the anode as well as nickel, manganese or cobalt oxides for the
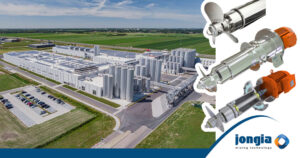
The Jongia Magitator: The solution for zero emission and leakage free mixing!
Side-entry agitators and mixers in the product range of Jongia Mixing Technology are the best fit for applications such as keeping dairy or starch products homogenous or keeping vegetable oil or juice storage on the right temperature. For these applications