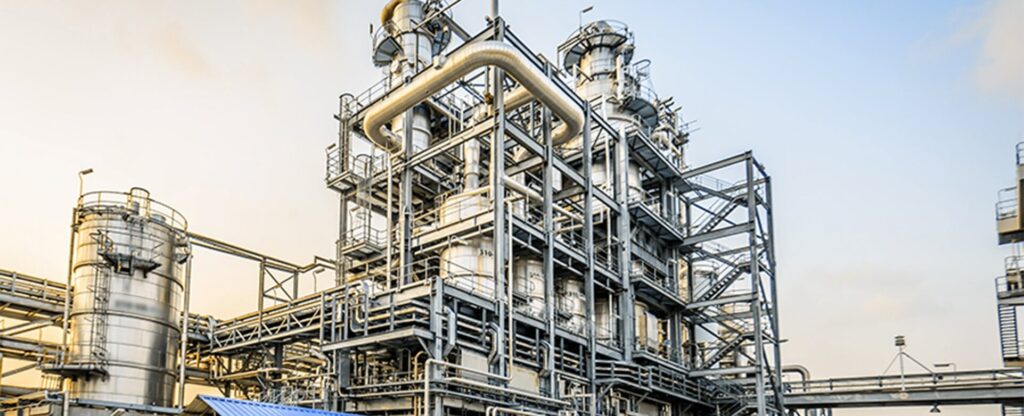
Chemical
Many years of experience enable Jongia to meet the stringent requirements of the chemical industry. Our mixers can be fitted with a variety of seals and special class E-motors to meet the very strict safety standards which often come with applications in the chemical industry.
Jongia’s stirring and mixing equipment comply with extreme criteria concerning emission values, shaft alignment tolerances and rotational accuracy.
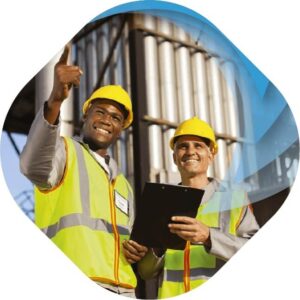
Proper mixer selection is vital to process optimisation, for that you can rely on our experienced staff of engineers and process technologists.
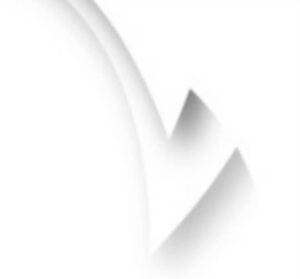
Our innovative side entry magnetic driven mixer, the Magitator, is very suitable for the Beverage industry due to its sealless design. Hermetically tight vessels promote hygiene and since there is no seal the risk of contamination is eliminated.
Chemical Applications
Frequently Asked Questions
What experience does Jongia have in the chemical industry?
Jongia has many years of experience serving the chemical industry, allowing them to meet stringent safety standards. We offer mixers with various seals and special class E-motors, ensuring compliance with strict safety requirements for chemical applications.
What types of mixers does Jongia offer for chemical applications?
Jongia provides stirring and mixing equipment designed to meet extreme criteria concerning emission values, shaft alignment tolerances, and rotational accuracy, tailored specifically for the chemical industry.
How does Jongia ensure process optimization for mixer selection?
Jongia emphasizes the importance of proper mixer selection for process optimization. We rely on our team of experienced engineers and process technologists to guide customers in selecting the right mixing solutions.
What innovations does Jongia offer in mixer designs?
Jongia’s Magitator is an innovative side-entry magnetic driven mixer, ideal for the beverage industry. Its sealless design promotes hygiene and eliminates contamination risks, making it a suitable choice for sensitive applications.
How does Jongia support the petrochemical industry?
Jongia’s mixers address key challenges in the petrochemical industry, such as BS&W management and heat transfer. Our team employs CFD analysis for effective tank mixing solutions, enhancing blending times and efficiency for fuel oils and other petrochemical products.
Chemical Industry Contacts
Contact our specialized team for all your questions
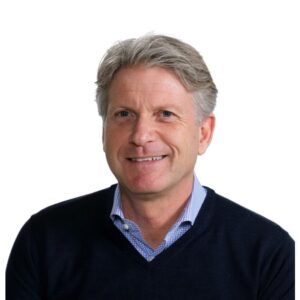
Tom Pruymboom
Sales Director
Area Worldwide
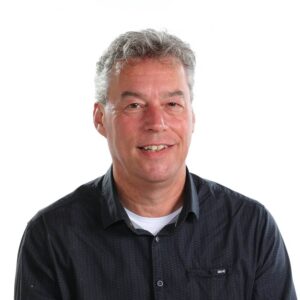
Bart Brouwer
International Sales Manager
Area Worldwide
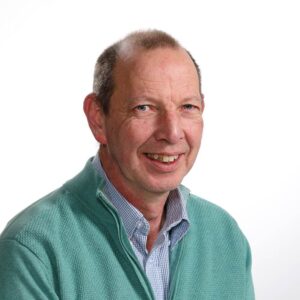
Jan Siert Tjeerdsma
Project Manager
Technical Specialist
Petrochemical
The petrochemical industry starts often with the storage of crude oil, waiting to be refined and processed. With the storage of the crude oil customers have to deal with BS&W (Basic Sediment & Water), heat transfer and homogenization issues. Jongia engineers have developed side entry mixers for these applications based on CFD (Computational Fluid Dynamics) analysis and know-how, resulting in the most effective and efficient induced flow in the tank.
Jongia engineers are able to calculate on blending time and tank cycles for additives on fuel oils, kerosenes and diesels. Given the current global energy transition these types of fuels are getting more and more important for the industry as well as for the end users.
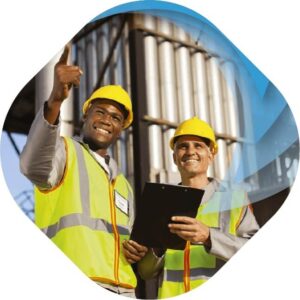
Maximum performance at minimum power input
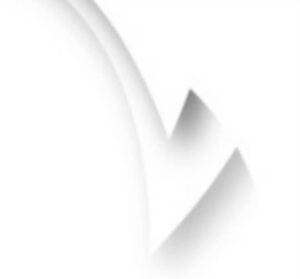
Further downstream where these products are being refined and processed to petrochemicals, Jongia has a lot of reference projects in monomers and polymers. From low viscous premix slurries to high viscous polymers in high pressure reactors, Jongia will design the most effective mixing element for best performance. Anchor type low speed mixing element will be challenged by a CRM geometry to gain the maximum output. In line dynamic mixing in Butyl-rubber process streams have been designed by our engineers for the most effective particle size (microns).
Jongia’s empiric know-how and theoretical knowledge results in the maximum performance and output of your process, based on the fact that we also make a cross reference on different technologies in another industry processes.
Petrochemical Industry Contacts
Contact our specialized team for all your questions
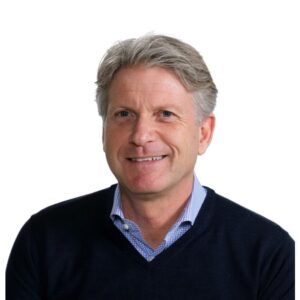
Tom Pruymboom
Sales Director
Area Worldwide
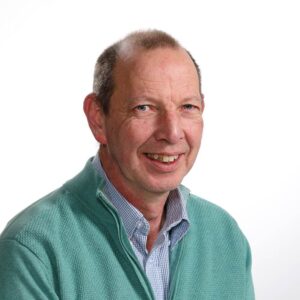
Jan Siert Tjeerdsma
Project Manager
Technical Specialist
Chemical – Related Articles
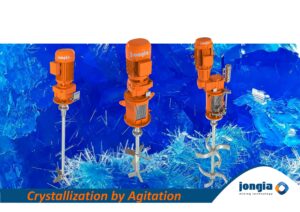
Difference between precipitation and crystallization
Precipitation and crystallization are both processes involved in the formation of solid substances from a solution, but they occur under different conditions and result in different outcomes. 1. Precipitation: Precipitation occurs when a solid substance forms from a solution as
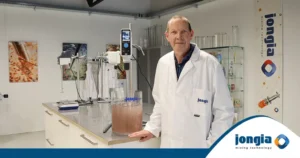
Tutorial: How does the Counterflow work?
The Counterflow is a very suitable mixing element for mixing processes of medium viscous liquid products such as paints, polymers and biodegradable plastics where starch is the basic component. In this tutorial we show you how the Counterflow moves the
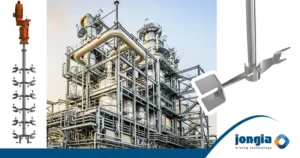
The Counterflow: from request to solution
Mainly in the chemical industry, the Counterflow mixing element is applied in mixing processes of products such as paint, polymers, biodegradable plastics where starch is the basic component and medium viscous liquids. However, what kind of questions do the customers