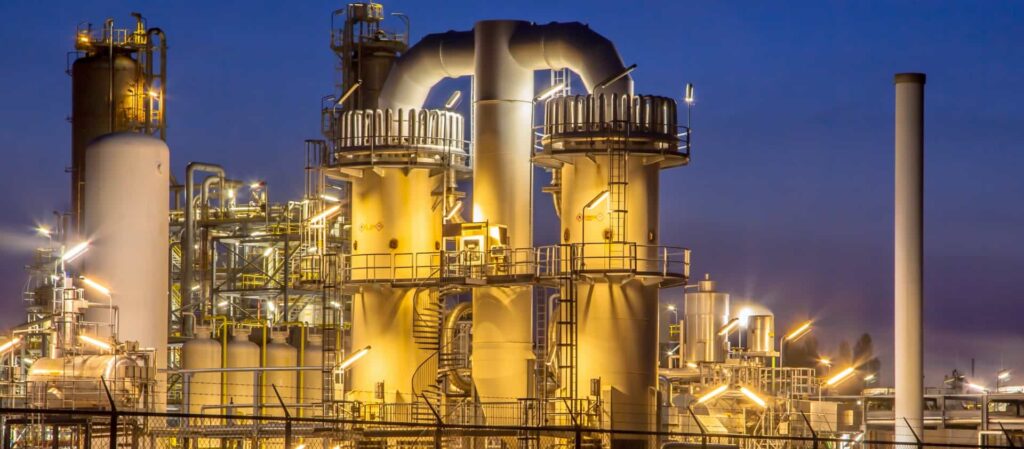
Chemical Tank Mixer
Chemical tank mixer: The ultimate guide for industrial agitators
Are you working in the chemical industry and looking for ways to improve your chemical mixing process? You are on the right spot, because a chemical tank mixer might be the solution you need! Chemical mixers come in various designs and sizes, and they play a crucial role in chemical processing by ensuring homogeneity, preventing sedimentation, and promoting chemical reactions.
In this blog post, we’ll provide you with a comprehensive guide to chemical tank mixers. We’ll discuss their types, applications, materials, motor and gearbox options, and other factors that affect their performance. We’ll also highlight the benefits of using chemical mixers in chemical processing and storage.
We will explore the duties, skills, and salaries of chemical mixers, the range of processes, batch documentation, and agitation solutions. We’ll also look into the challenges that arise in the chemical industry, including the use of hazardous materials, company requirements, and company policies. But we first start with the basics. What does chemical mixing or chemical processing mean?
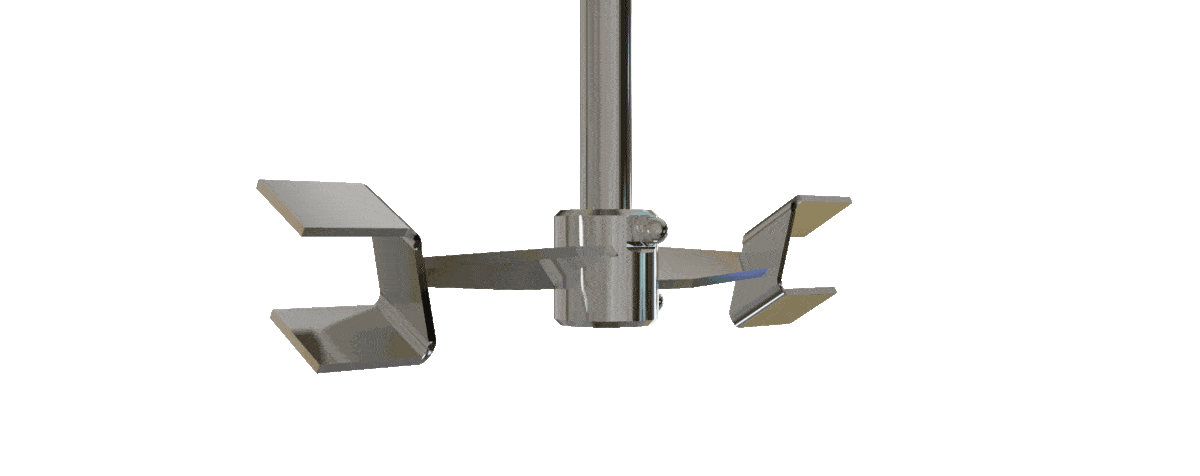
What types of chemical tank mixers do we have?
- Axial Flow Impellers: Axial impellers are designed to create axial flow, which is when the fluid moves in the same direction as the impeller’s rotation. These types of mixers are ideal for low-viscosity liquids, and they offer high pumping rates with low power consumption.
- Gas Dispersion Impellers: These impellers are used to disperse gas into liquids, which is critical in gas-liquid reactions such as hydrogenation and oxidation. Gas dispersion impellers create a high degree of turbulence and shear, leading to efficient mixing and mass transfer.
- Double Blade Mixers: Double blade mixers have two blades rotating in opposite directions, creating a shearing effect that promotes mixing and homogenization. These mixers are ideal for high-viscosity liquids and are commonly used in the food, cosmetic, and pharmaceutical industries.
- Straight Blade Turbines: Straight blade turbines create a radial flow, which is when the fluid moves perpendicular to the impeller’s rotation. These mixers are suitable for low to medium viscosity liquids, and they’re commonly used in chemical processing and wastewater treatment.
Materials used in chemical tank mixers
Chemical tank mixers are made of different materials, depending on the application and the type of chemicals being mixed. Here are some of the common materials used in chemical mixers:
- Stainless Steel: Stainless steel is a popular choice for chemical mixers due to its high resistance to corrosion and durability. 304 stainless steel is commonly used for basic storage options, while 316L stainless steel is used for more aggressive chemical tank applications.
- Carbon Steel: Carbon steel is also commonly used in chemical mixers due to its high strength and resistance to abrasion. However, it’s not as resistant to corrosion as stainless steel and requires a protective coating to prevent rust.
- Plastic Mixing Tanks: Plastic mixing tanks are an attractive option for chemical mixers due to their chemical resistance, light weight, and lower cost. Poly processing, U.S. Plastic Corp., and Hypro pump are some of the popular brands that offer plastic mixing tanks for chemical mixing applications.
Motor and gearbox options for chemical tank mixers
The motor and gearbox options for chemical tank mixers play a crucial role in their performance and energy efficiency. Here are some of the motor and gearbox options available:
- Electric Motor: Electric motors are the most common motor type for chemical mixers, and they come in different sizes and power ratings. They’re easy to operate and provide high torque at low speeds, making them ideal for heavy liquids and high-viscosity liquids.
- Cage Motors: Cage motors are a type of electric motor that provides high starting torque and low operating noise. They’re ideal for large chemical tanks and heavy-duty applications.
- Motor and Gearbox: The motor and gearbox combination is a popular option for chemical mixers as it provides high torque at low speeds, leading to energy efficiency and reduced wear and tear on the equipment. The gearbox also helps to reduce the speed of the impeller, leading to more efficient mixing and better homogeneity.
Applications of chemical tank mixers
Chemical tank mixers are used in a wide range of chemical processes, including chemical blending, chemical storage, and chemical reactions. Here are some of the common applications of chemical mixers:
- Chemical Blending: Chemical blending involves mixing two or more chemicals to create a homogeneous mixture. Chemical mixers ensure that the chemicals are thoroughly mixed, preventing sedimentation and promoting chemical reactions.
- Chemical Storage: Chemical mixers are also used in chemical storage tanks to prevent sedimentation and ensure that the chemicals remain homogeneous. They also help to reduce the potential damage caused by settling and promote energy-efficient heat transfer.
- Chemical Reactions: Chemical mixers play a crucial role in chemical reactions by promoting mixing and ensuring that the reactants are thoroughly mixed. This leads to more efficient chemical reactions and reduces the processing time.
Now you know that chemical mixers can be used in a variety of applications, we move on to the several benefits it offers.
What are the benefits of using chemical tank mixers?
Chemical tank mixers offer several benefits to chemical manufacturers and processors, including:
- Improved Efficiency: Chemical mixers ensure that chemicals are thoroughly mixed, leading to more efficient processing and reduced processing time.
- Improved Homogeneity: Chemical mixers prevent sedimentation and promote homogeneity, leading to consistent product quality and reduced waste.
- Reduced Maintenance: Proper mixing reduces wear and tear on the equipment, leading to reduced maintenance costs and increased equipment lifespan.
- Energy Efficiency: Chemical mixers with energy-efficient motors and gearboxes help to reduce energy consumption and operating costs.
- Customization: Chemical mixers come in different sizes, designs, and materials, allowing for customization to suit specific applications and processes.
Conclusion
Chemical tank mixers are an innovative component in the chemical industry, and they play an important role in ensuring efficient processing, storage, and reactions. With decades of industry experience, Jongia Mixing Technology offers a wide range of product selections. By understanding the different types of chemical mixers, their applications, materials, motor and gearbox options, and benefits, chemical manufacturers and processors can make informed decisions on the best mixer for their needs. We hope you have found the information you were looking for. If not, please get in touch with us to find the solution you need.Contact our specialized team for all your questions
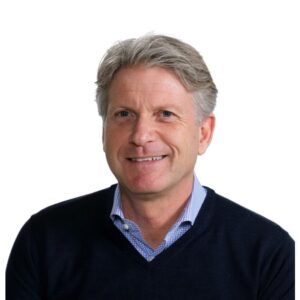
Tom Pruymboom
Sales Director
Area Worldwide
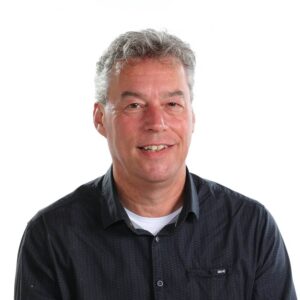
Bart Brouwer
Area Sales Manager
Area Worldwide
Technical Questions?
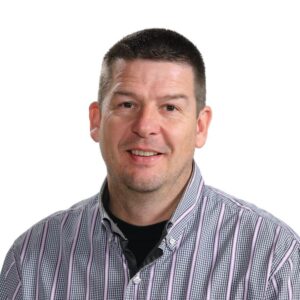
Sijko van der Veen
Application Engineer
Technical Specialist
Popular Posts
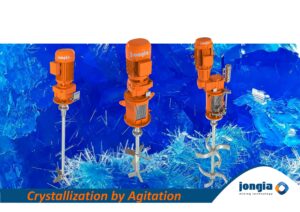
Difference between precipitation and crystallization
Precipitation and crystallization are both processes involved in the formation of solid substances from a solution, but they occur under different conditions and result in different outcomes. 1. Precipitation: Precipitation occurs when a solid substance forms from a solution as
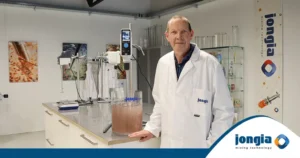
Tutorial: How does the Counterflow work?
The Counterflow is a very suitable mixing element for mixing processes of medium viscous liquid products such as paints, polymers and biodegradable plastics where starch is the basic component. In this tutorial we show you how the Counterflow moves the
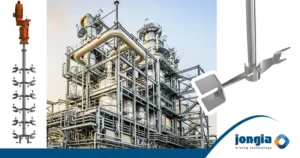
The Counterflow: from request to solution
Mainly in the chemical industry, the Counterflow mixing element is applied in mixing processes of products such as paint, polymers, biodegradable plastics where starch is the basic component and medium viscous liquids. However, what kind of questions do the customers