Article Leeuwarder Courant 25 May 2016, photo: Catrinus van der Veen
The new manure digester at the Dairy Campus will soon be up and running. There is a glimmer of hope for farmers and municipalities.
Until mid-2012, cows from the Dairy Campus heated the houses in Techum. The manure of the animals was fermented together with corn and the biogas was transported to the new housing estate in Leeuwarden where it was used to produce electricity and heat. But due to technical problems and high corn prices, Dairy Campus pulled the plug on the digester that year and the people of Techum had to make do with regular natural gas.
In August, it’s the cows’ turn again. The American companies Evergreen Energy and Clark Technology, together with Universal Energy Solutions of the Leeuwarden entrepreneur Piet van der Hoop and the Fûns Skjinne Fryske Enerzjy, have united to form Biogas Leeuwarden and have a brand new manure digester built on the same site. Equipped with a technology by which cow manure can be profitably fermented. Production will start in June and by August there should be enough biogas available for Techum.
Woody substances
The special feature of the digester is that the plant is able to extract biogas from woody substances such as twigs, leaves, wood chips and roadside grass. This has been demonstrated on a smaller scale in the Evergreen Energy installation. The project at the Dairy Campus must demonstrate whether this technology also works on a large scale.
Before ending up in the digester, the cow manure, roadside grass and twigs are first ground in a so-called biogrinder and transferred to a hydrolysis tank where the cell structure is broken open. The latter enables the bacteria to make better use of the material and produce more biogas with a higher methane content. Also new in the digester are the mixers, made by Jongia in Leeuwarden, which ensure a continuous mixing of the substance to be digested, emphasizes director Wim Vrieling of Biogas Leeuwarden.
Twice as much biogas
The hope and expectation is that the U.S. manure digester will produce twice as much biogas as its predecessor: 1,000 cubic meters per day instead of 500. The goal is to upgrade half of the biogas production to natural gas quality and inject it into the gas grid.
If the digester functions properly, it offers prospects, especially for livestock farmers and municipalities. The farmers no longer need to use food, such as corn, and they are no longer dependent on expensive by-products. Municipalities will be much cheaper with their green waste. The initiators are confident. They are aiming at a global market, Vrieling knows.
Similar projects are in preparation in Ukraine, Turkey and some African countries.
Contact our specialized team for all your questions
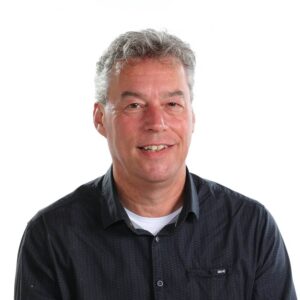
Bart Brouwer
Area Sales Manager
Area Worldwide
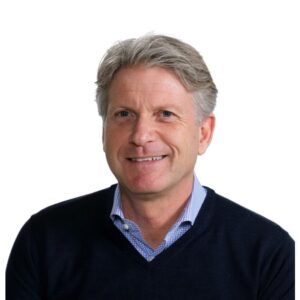
Tom Pruymboom
Sales Director
Area Worldwide
Technical Questions?
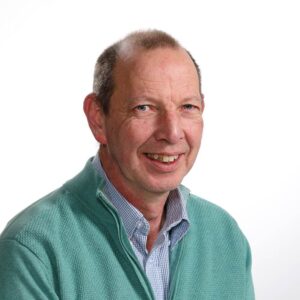
Jan Siert Tjeerdsma
Project Manager
Technical Specialist
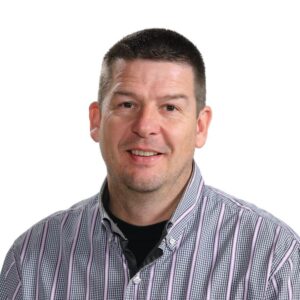
Sijko van der Veen
Application Engineer
Technical Specialist
Related Articles
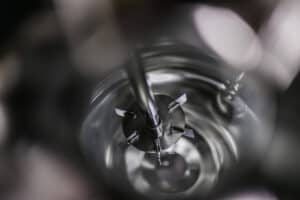
Jongia Mixing Technology Agitators in Process Installations
This reactor setup from Veenbrink RVS, equipped with Jongia agitators, forms the foundation for polymer production. The system is applied in an ATEX classified zone: the equipment zone 1 IIB T2, whilst the space itself is designated as zone 2
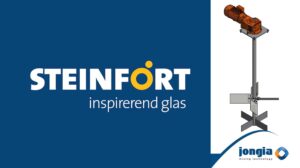
Steinfort Glass selects Jongia Mixing Technology
Meet Mr. Gerlof Reineker, general manager of Steinfort Glas in Franeker. Steinfort Glass specializes in processing flat glass for various applications. The company purchases large sheets of glass and processes them into products such as shower doors, office glazing, bus
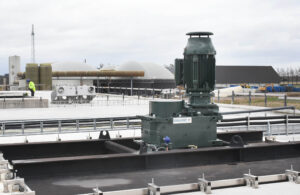
Jongia agitators with Nord Maxxdrive gearboxes for Smits Group biogas plant
Jongia Mixing Technology recently delivered a series of agitators with Nord Maxxdrive gearboxes for the biogas plant of Brabant-based agricultural company Princepeel, part of the Smits Group. These ‘heavy duty’ Agitators optimally withstand the high torques required to move the