Biodiesel Blends
The term “biodiesel” is often used interchangeably with “renewable diesel,” although there are some differences. Renewable diesel refers to biofuel produced from vegetable oils or animal fats; while biodiesel is derived from plant sources such as soybeans, rapeseed, palm oil, or jatropha.
There are three main types of biodiesel blends: B0 (no biodiesel), B5 (up to five percent biodiesel), and B20 (six to twenty percent biodiesel). Pure biodiesel is usually reserved for use in stationary applications like heating equipment where it provides a cleaner burning alternative to petroleum based fuels. In addition, pure biodiesel is sometimes used in heavy duty vehicles where its low viscosity makes it easier to inject into engines.
In general, biodiesel blends tend to perform better in colder climates because the cold temperatures slow down chemical reactions that cause combustion problems. However, biodiesel blends can also be problematic in warmer areas due to increased emissions during start up and shut down operations.
Blending biodiesel with diesel fuel isn’t a picnic in the winter
The oil industry is booming. As demand increases for biofuels like ethanol and biodiesel, there’s been a corresponding increase in the number of refineries popping up across the United States. And now, thanks to a recent decision by the Environmental Protection Agency, more people are turning to biodiesel blends — those mixtures of vegetable oils and petroleum products that contain less carbon dioxide emissions than pure fossil fuels.
But blending biodiesel with diesel fuel doesn’t come without drawbacks. For starters, you don’t want to mix the two types of fuel in cold weather because the blend could start separating out, causing problems with engines.
How Does Biodiesel Blending Work?
The process of making biodiesel begins with the conversion of vegetable oil into fatty acid methyl esters (FAME). This is done through a chemical reaction called transesterification. The FAME are separated from glycerin, water, and soap produced during the reaction. After separation, the FAME must undergo further processing to become usable biodiesel.
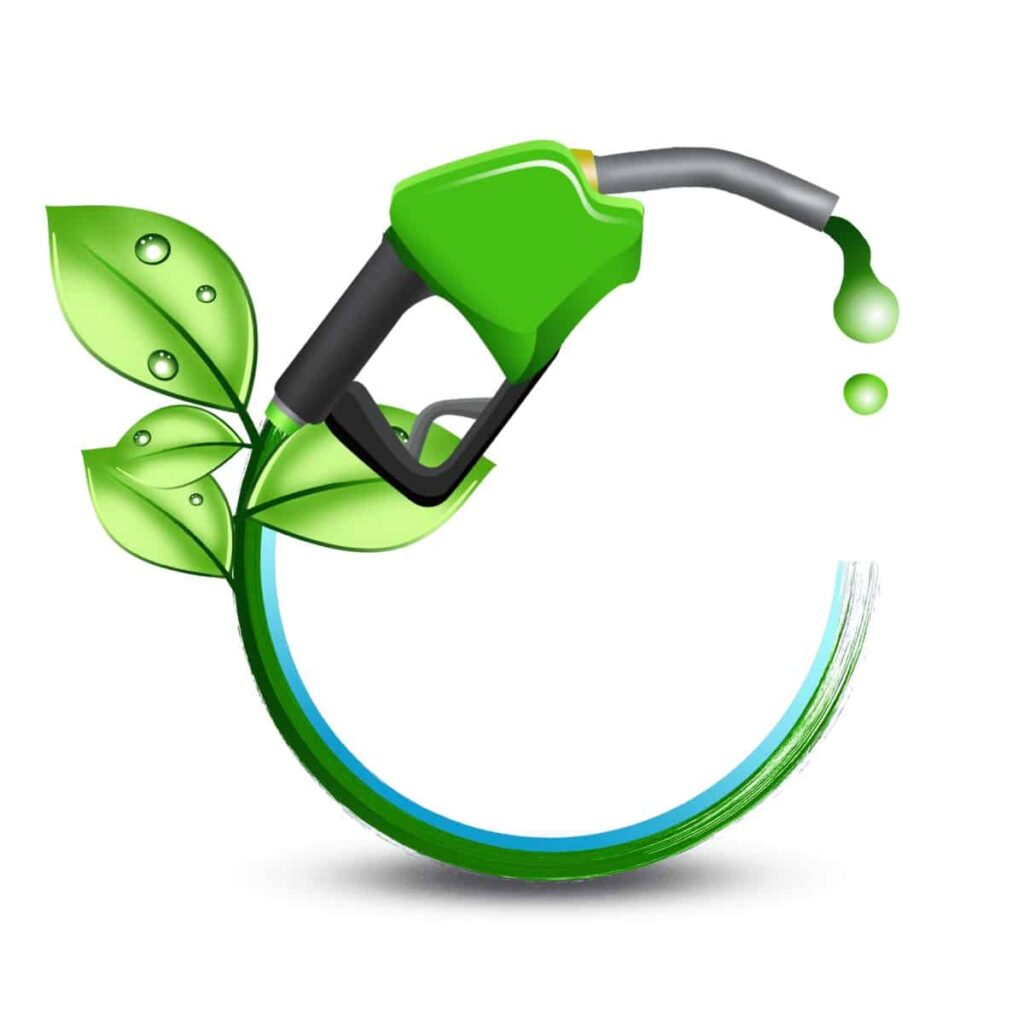
There are four main ways to make biodiesel: splash, tank, inline, and rack injection blending, each of which has different requirements.
Splash Blending
With biodiesel, there are a few different options for blending. Biodiesel can be blended with conventional petroleum-based diesel fuel or even used alone. Splash blending refers to the process of mixing biodiesel with conventional diesel fuel prior to filling the storage tanks. Splash blending allows for a more homogeneous mixture that reduces the likelihood of sedimentation within the container.
The process involves adding the biodiesel to the tank containing the conventional diesel fuel and agitating the contents while allowing the diesel fuel to drain out. Once the biodiesel is drained, the remaining diesel fuel is added to the tank. The process is repeated until the desired amount of biodiesel is mixed with the conventional diesel fuel.
In-Tank Biodiesel Blending
Fuel blending is a critical component of biodiesel production. A properly blended fuel can increase energy efficiency, reduce emissions and improve performance. However, it can be difficult to achieve consistent fuel quality during blending due to differences in storage tanks, pumps, piping, etc. This article provides information about how to blend biodiesel in-tank without causing problems such as foaming, sedimentation, emulsion formation, and poor combustion properties.
In-Line Blending
With in-line blending, biodiesel is added to the stream of diesel fuel as the two products travel through a pipe or hose, mixing together as they go. This method is used primarily where there are no facilities to store large quantities of biodiesel. In-line blending reduces the cost of transportation because it eliminates the need to transport large volumes of biodiesel separately.
Rack Blending
The process of blending biofuels, such as ethanol, biodiesel, and vegetable oil, is called “rack blending.” This method allows customers to add it directly to existing fuel tanks, rather than having to retrofit trucks. Biofuel blends are already used in some areas of the USA, including California, Colorado, Kansas, Louisiana, Minnesota, Nebraska, New Mexico, North Dakota, Oklahoma, South Carolina, Texas, Utah, Virginia, Washington, Wisconsin, Wyoming, and Guam.
In addition to reducing emissions, rack blending reduces costs because there is no need to buy expensive new equipment. One study found that adding 10% biodiesel to conventional diesel could save up to $1 million per truck. In addition, biofuel blends reduce corrosion, improve cold weather starting, increase torque, and provide better lubrication.
Cold Weather Blending
The coldest winter months bring about some challenges when blending fuels. Conventional distillate fuel blends freeze easier than biodiesel because of the lower flash points of the former. However, biodiesel can be blended into conventional distillate without causing problems. Biodiesel blends can be stored above ground in most climates. Below ground storage requires special care during cold weather.
Precautions may include protecting tank pipes and pumps. If you plan to use heating systems, make sure they are set up properly.
Contact our specialized team for all your questions
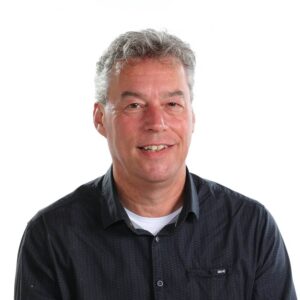
Bart Brouwer
Area Sales Manager
Area Worldwide
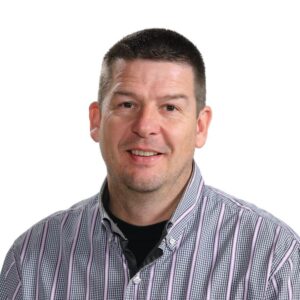
Sijko van der Veen
Application Engineer
Technical Specialist
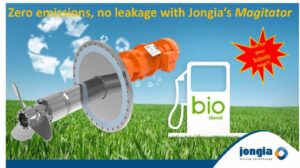
Biodiesel blending with zero leakage!
Fuel blending is a critical component of biodiesel production. A properly blended fuel can increase energy efficiency, reduce emissions and improve performance. However, it can be difficult to achieve consistent fuel quality during blending due to differences in storage tanks,
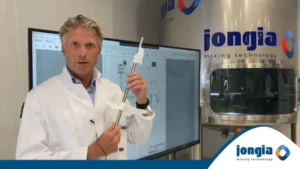
Tutorial: How does the BioFoil® propeller work?
The BioFoil® propeller is not just any propeller. It is Jongia Mixing Technology’s own design for the Biogas market. In the Biogas process gas is generated and disposed of from a tank filled with liquid (digestate). Recently, this technique has
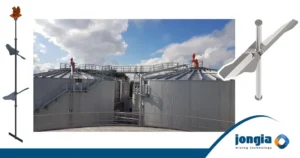
The development of a proprietary biogas agitator
Jongia Mixing Technology has been active in the biogas market since 2008. In the process regarding biogas, gas is generated and disposed of from a tank filled with fluid (digestate). This digestate mainly consists of organic waste. Over the last