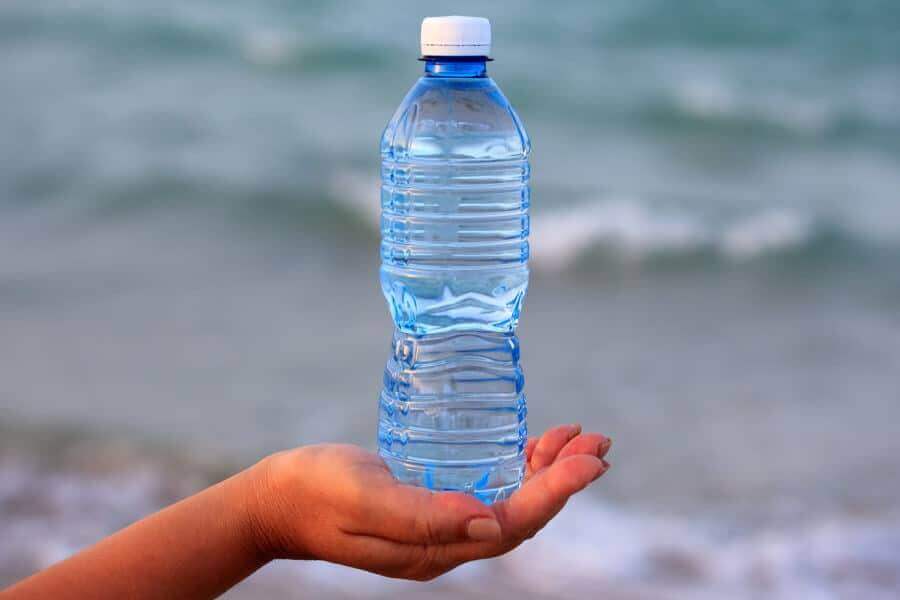
Plastics
Plastic is a plastic material that can be formed, through the application of heat and pressure. Thanks to this property of plasticity, often combined with other special properties such as low density, electrical conductivity, transparency and toughness, plastics can be made into a wide variety of products. Some such products include strong and lightweight beverage bottles made of polyethylene terephthalate (PET), flexible garden hoses made of polyvinyl chloride (PVC), insulating food containers made of foamed polystyrene and shatterproof windows made of polymethyl methacrylate.
The relatively inexpensive production cost of plastic is one reason why it is so hugely popular. Plastic products are also popular with businesses, for example, plastic packaging for product agents, plastic bags at local retailers and the use of plastic for new products. Plastic is everywhere, the downside of this is that there is a very large amount of plastic litter. Much of this plastic litter ends up in the ocean, among other things, which has a huge impact on the environment.
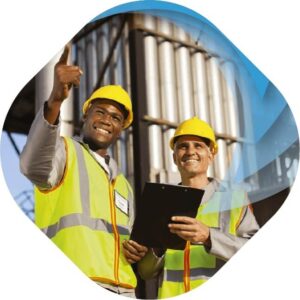
Maximum performance at minimum power input
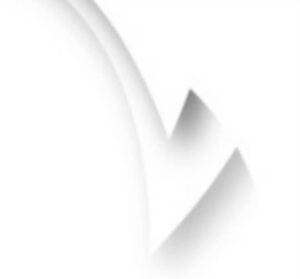
Recycling of plastics
With consumer awareness comes a much greater focus on recycling plastic. Because of the enormous consumption and production of plastic, a lot of plastic litter is also created indirectly. Many plastic products are made for single use, given the new environmental trends, manufacturers are increasingly working to reduce the waste of raw materials. By recycling different types of plastic with each other, you give plastic products a new life. With this way of producing new plastic from previously used plastic, the impact on the environment is reduced a lot.
The market development of plastic
The global plastics market was valued at $593.00 billion in 2021. Of this, the market is only expected to grow further in the coming years. This is because the demand for quantity of plastic continues to rise, the growth in demand for plastic is mainly due to increasing plastic consumption in construction, automotive and electronic energy.
Frequently Asked Questions
What are the main properties of plastics?
Plastics are known for their plasticity, which allows them to be molded with heat and pressure. They also have unique properties such as low density, electrical conductivity, transparency, and toughness, making them suitable for a wide variety of products like beverage bottles and garden hoses.
Why is plastic so widely used?
The relatively low production cost of plastic contributes to its popularity. Businesses often favor plastic for packaging, bags, and various products due to its versatility and affordability, which has resulted in its significant presence across many industries.
What are the environmental concerns related to plastic?
A major concern with plastic is its extensive littering, much of which ends up in oceans, harming wildlife and ecosystems. The widespread use of single-use plastics exacerbates this issue, leading to increased waste and environmental impact.
How does plastic recycling work?
Recycling involves reprocessing used plastics into new products, reducing the need for raw materials. This practice decreases environmental impact by minimizing waste and energy consumption associated with creating new plastic from virgin materials, thus giving plastics a new life.
What is the current market trend for plastics?
In 2021, the global plastics market was valued at $593 billion and is expected to continue growing. The demand for plastic is primarily driven by increased consumption in sectors such as construction, automotive, and electronics, indicating robust market development.
Petrochemical Industry Contacts
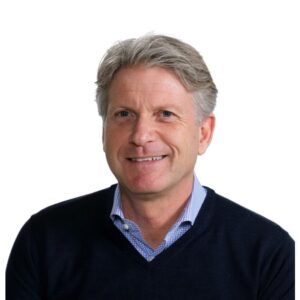
Tom Pruymboom
Sales Director
Area Worldwide
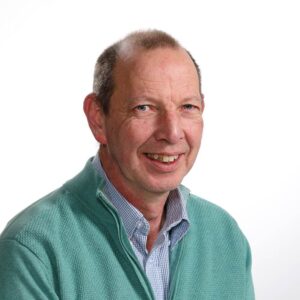
Jan Siert Tjeerdsma
Project manager
Technical Specialist
Petrochemical – Related Articles
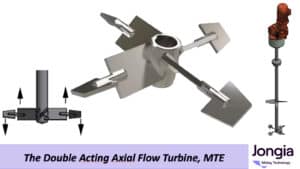
The Double Acting Axial Flow Turbine type AST-MTE mixing element
Operation of an AST-MTE Element Operation of an AST-MTE Element This element can be used in both CW (clockwise) and CCW (counterclockwise) directions. In one case, the inner AST element is downward-pumping with the outer tips pumping upward, and in
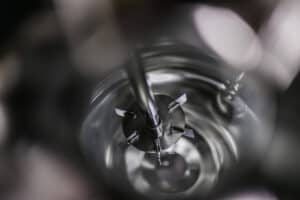
Jongia Mixing Technology Agitators in Process Installations
This reactor setup from Veenbrink RVS, equipped with Jongia agitators, forms the foundation for polymer production. The system is applied in an ATEX classified zone: the equipment zone 1 IIB T2, whilst the space itself is designated as zone 2

A New MD for Jongia Mixing Technology!
Leeuwarden, 23 April 2025 We are delighted to announce that we have a new Managing Director at Jongia Mixing Technology! Our new MD is Mr. Jean Philippe Pfeiffer. Jean Philippe has worked for De Dietrich for 29 years as Group
Polymers
Polymers, also known as plastics, are being produced in large industrial volumes. Each manufacturer has its own specific process conditions, though the principle is always the same.
The most known and commercially worldwide produced plastics are Polyethylene (PE) and Polypropylene (PP).
Depending on the production process either High Density PE or Low Density PE can be produced. For the production of polyethylene the process steps can be described as follow:
- Distillation
- Cracking
- Polymerization
- Blending
Atmospheric Distillation
In the first step of this process, crude oil will be heated and guided to a distillation column were the lighter fraction (propene, butane) evaporates. The middle fractions (such as naphtha, kerosene, gasoil) are being taken away for further treatment in other refinery units. The Nafta will be the feed for the next process step.
Cracking
The Nafta is now treated with steam up to temperatures of 875 °C. Nafta will be “cracked” into small size molecules, unsaturated hydrocarbons, such as Ethene, Propene and Butene. These gasses are been separated from each other and the Ethene is guided to a polymerization reactor.
Polymerization
By means of polymerization, polyethene is created in a reactor. This can be done via (free-radical) polymerization at extreme high pressure and high temperature. It has an open structure and is called Low Density polyethylene LDPE. This polymer is soft, transparent en not very strong. Finaly for customers used as bottles, plastic bags etc.
Finally the polyethylene molecules are kept in a residence time pot, to terminate the polymerization reaction. Jongia has designed and manufactured mixers for this type of process and reactors. Reactors/mixers having a design Temperature of 100C and a design Pressure of 5000 kPa. Viscosities generally in the range from 600 – 3500 cP.
The purpose of the mixers is to mix the residence time pots and the slurry feed tanks. Jongia has selected a HDM type for this process, with a coaxial gearbox and flexible coupling between drive en motor. Together with a magnetic coupling (design pressure 50 Barg) this mixer is highly effective as well as efficient.
The mixer type HDM is designed for heavy duty industrial applications. Due to the 2 (or even 3) bearing sections, the HDM type can have relatively long shafts, without bottom bearing. Due to the flexible coupling and double bearing sections, the radial and axial loads are completely absorbed.
References:
LyondellBasell, Sabic, DSM, Ineos, Dow Chemicals, Lanxess