Current commercial lithium ion batteries mainly contain transition metal oxides or phosphates, aluminum, copper, graphite, organic electrolytes containing harmful lithium salts, and other chemicals. Therefore, the recycling and reuse of spent lithium ion batteries has been paid more and more attention by many researchers.
However, due to the high energy density, high safety and low price of lithium ion batteries have great differences and diversity, the recycling of waste lithium ion batteries has great difficulties.
Besides the material which can be regenerated by means of recycling, The electrolyte in the LIBs also contains harmful substances, such as organic solvents and fluorine-containing lithium salts, which may cause great harm to the environment.
Therefore, if spent Lib’s directly puts in the environment, it will cause an irreversible environmental disaster. In addition, the high-priced metals contained in LIBs, such as Li, Co, Ni, Cu & Al, also have good resource value
In view of the above reasons, the recycling of spent Lib’s has a considerable prospect and is environmentally friendly, so it is imperative to establish a reasonable recycling system and develop related recycling technologies.
Generally, a Lib includes a cathode, an anode, a separator, electrolyte, and a can with a sealing function.
The image shown below is explaining the different components, from which the most important ones to recycle and regenerate are:
The Cathode active material & the Anode active material
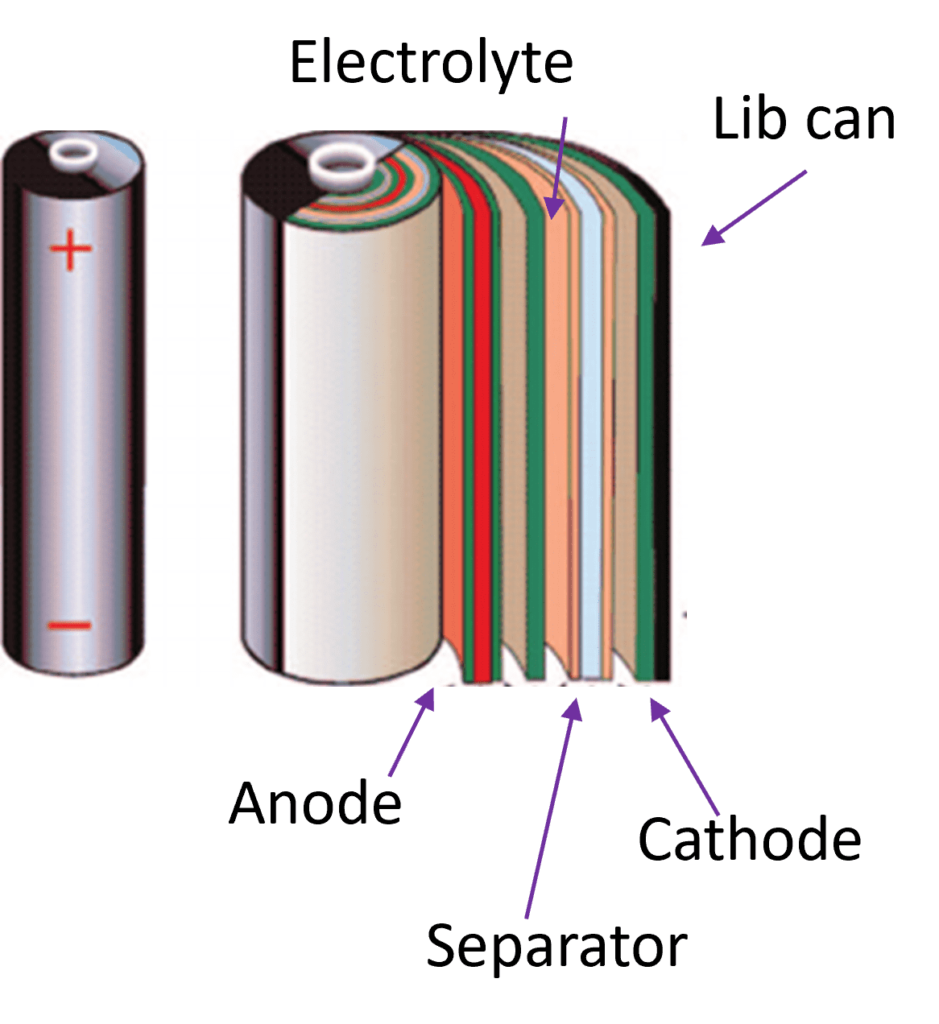
The Methods of Recovering Lithium Ion Batteries
Recycling for LIBs usually involves both physical and chemical processes. Due to the complex assembly process of LIBs and the wide variety of electrodes, it brings great danger for the recovery of battery. The explosion, combustion and poisonous gas brought on the recovery process are easy to cause casualties.
To reduce this risk, spent LIBs usually need to be discharged before recycled. Physical processes usually include pretreatment and direct recovery of electrode materials. These processes usually include disassembly, crushing, screening, magnetic separation, washing, heating treatment, etc.
First the batteries need to be disassembled
Disassembly, usually takes place with shredders to break down the batteries and separate the black mass, which is later-on filtered, washed and dried to recover valuable raw material, such as lithium, cobalt, or graphite.
Very important to understand is that recycling these raw materials instead of simply dumping old batteries on landfill sites, saves our environment.
One of the most common recycling processes for the active material components is the hydrometallurgical process. This process usually involves leaching, separation, extraction and chemical / electrochemical precipitation.
Hydrometallurgical Process
Nowadays hydrometallurgy is typically used to recover LIBs after pretreatment. According to the physical properties of the materials in the spent LIBs, including morphology, density, and magnetism, etc. The treated battery cases, electrodes and membranes containing electrolytes will be treated separately to improve the safety and recovery rate of hydrometallurgical processes and reduce energy consumption during the use of hydrometallurgical or pyrometallurgical recovery electrode materials.
The hydrometallurgical process is considered to be the most suitable method for the recycling of spent lithium-ion batteries. A more flexible and universal process in the future is required for the recovery of different types of spent lithium-ion batteries. Besides cathode active materials, the other components of spent lithium-ion batteries including electrolyte and anode materials also need to be recovered due to their potential environmental hazards.
Hydrometallurgy can be defined as a metal recovery method used to obtain metals from ores and waste materials using aqueous media by combining water, oxygen, and other chemical reagents with or without the use of a pressurized environment.
Key process steps
Schematic of the recycling procedure at an industrial scale, based on the principles of direct recycling. Cell packaging of the Lib’s is first removed before the entire cell stack is processed in a solution without further component separation. Solids and liquids are then separated and recovered for direct regeneration via thermal annealing for the solid electrolyte and direct re-lithiation for the cathode.
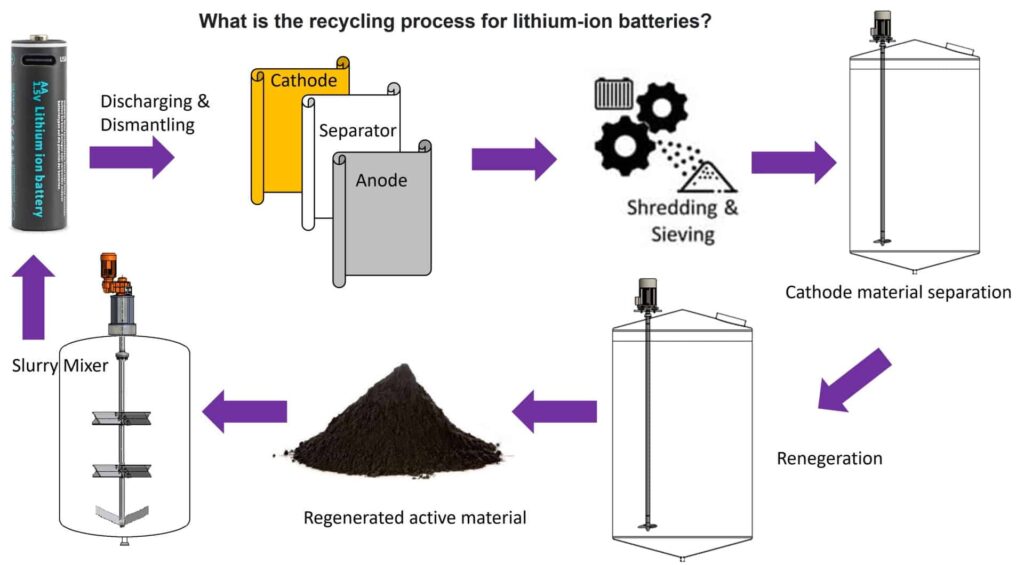
When it comes to leaching
Hydrometallurgy involves leaching and reduction. It is usually divided into acid leaching and biological leaching according to the leaching method.
Below image is showing the application of oxalic acid leaching to regenerate Li(Ni1/3Co1/3Mn1/3)O2 (NCM) cathodes from spent LIB’s.
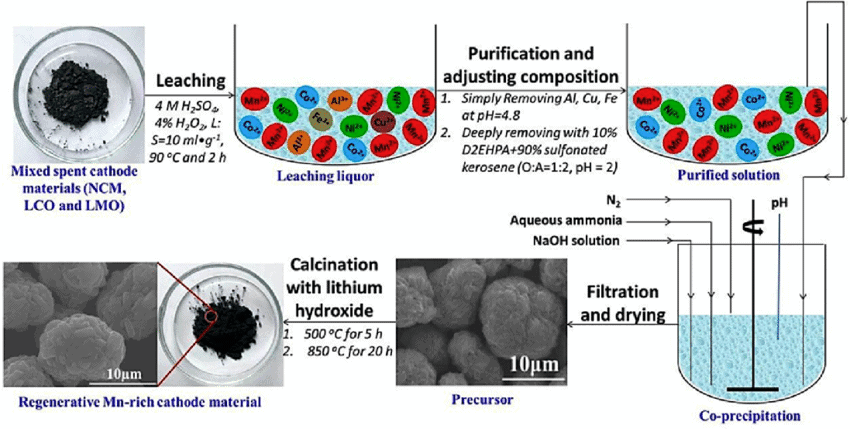
With lithium dissolving into the solution, the transition metals transform into oxalate precipitates and deposit on the surface of spent NCM cathodes, separating lithium and transition metals in one simple step. After mixing with a suitable agitator, certain amount of Li2CO3, the oxalate precipitates together with unreacted NCM are directly calcined into new NCM cathodes. This process is called: Regeneration.
Regenerated NCM exhibits the best electrochemical performances, delivering the highest initial specific discharge capacity of 168 mA h g–1 at 0.2C and 153.7 mA h g–1 after 150 cycles with a high capacity retention of 91.5%. The excellent electrochemical performances are attributed to the sub-micrometer particles and voids after calcination, as well as the optimal proportion of elements. This process can make the most of valuable metals in the spent cathodes, with >98.5% Ni, Co, and Mn recycled. It is simple and effective, and provides a novel perspective of recycling cathodes from spent LIBs.
Jongia Mixing Technology has been involved in many Lib’s recycling projects and has successfully supplied many Agitators and Mixers for these applications.
This due to the long existing experiences Jongia has achieved with many parties in the recycling and regeneration industry. Once fluids are present in the process, whether these are for common applications or for hazardous applications with reactors, high temperatures and pressures, reliability is very important. That is the reason, the recycling and regeneration industry has chosen Jongia to design and build the suitable agitator for their process.
In the examples of the Cathode material separation, the leaching and the slurry production for new active material, Jongia Mixing Technology has selected mixing elements such as hydrofoils, propellers and other mixing element combinations to design the most optimized mixer for the requested volumes, material capabilities and selected material alloys from which the mixers are produced in Jongia’s production site in Leeuwarden, The Netherlands.
Jongia Mixing Technology is always able to assist in the selection for the agitator configuration. Just contact Jongia and ask for assistance.
We are always available for your mixer requests.
Contact us at: info@jongia.com or visit our Battery Page for more Ion-Lithium battery related articles.
Contact our specialized team for all your questions
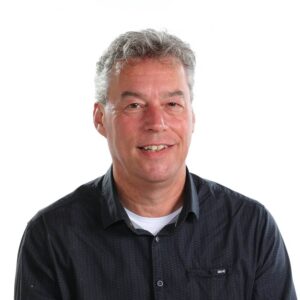
Bart Brouwer
Area Sales Manager
Area Worldwide
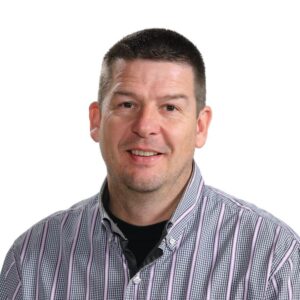
Sijko van der Veen
Application Engineer
Technical Specialist
Technical Questions?
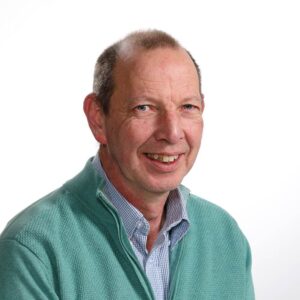
Jan Siert Tjeerdsma
Project Manager
Technical Specialist
Related Articles
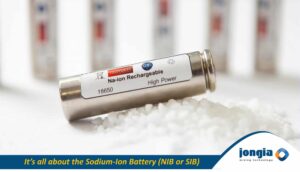
Is Sodium-Ion the next generation sustainable Battery?
The sodium-ion battery (NIB or SIB) is a type of rechargeable battery that uses sodium ions (Na+) as its charge carriers. Its working principle and cell construction are almost identical with those of lithium-ion battery (LIB) types, but replace lithium with sodium.
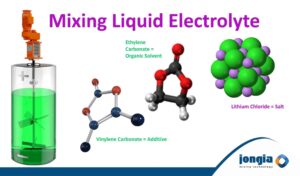
Mixing Electrolyte for Ion-Lithium Batteries
Electrolyte as basis for Ion-Lithium Batteries plays a key role in transporting the positive lithium ions between the cathode and anode, and consequently the charging and discharging performance of the battery. Hence, it needs to be checked for potential impurities.

Mixing the correct Ion-Lithium Battery Slurry is a real challenge!
Lithium-based battery technologies for electric vehicles use lithium-ions as the charge carrier. Depending on the application’s technical requirements, lithium is used with various chemistries such as graphite for the anode as well as nickel, manganese or cobalt oxides for the