Does the agitator fully meet the requirements? Are the dimensions of the agitator 100% in accordance with the technical drawings? When it concerns a complex agitator, a 3D scan is performed. This is done in order to guarantee the quality of an agitator and to be able to check the dimensions of the agitator during the production process. To do so, Jongia works together with Brandsma Digital Measurement (BDM), a company located in Bolsward.
Why a 3D scan?
A 3D scan is used to perform an exact dimensional check on complex shapes, for example an agitator. The agitator in this example has a double-formed ribbon and a minimum tolerance for free play towards the tank wall. It is important to know whether the dimensions of the agitator are within the set tolerances. The scan shows at an early stage whether the formed ribbon is the right size and whether the specified design requirements are guaranteed.
A 3D scan is generally used in two situations:
In the preliminary stage, to map an existing product or a certain situation and then be able to deliver the exact same (reverse engineering).
As a means of quality control, as is the case in this example. At an early stage it is checked whether the product has been manufactured entirely in accordance with the design.
How does the 3D scan work?
Distances are measured very precisely with laser technology. The laser tracker measures up to 0.1 mm accurately at a distance of 10 meters, from one location and thus has a wide range. An average measurement does not take much time, therefore a large amount of very exact data is generated in a short timeframe. The laser measures the exact size of the agitator point by point, which is also translated into a 3D point. All measuring points together form a pattern that resembles a 3D photo, only in this case executed on actual dimensions. When a scan has been performed on different sides of the object, the images are linked and a single image is created, including all measured distances. After this, a point model is made from the point measurement, called a mesh, which Jongia can import into its own 3D software. The scanned model can now be laid on top of the designed model for a final check. Execution and dimensions are checked in this way.
Certainty thanks to the 3D scan
Thanks to the scan, the customer is assured of an agitator that meets the requirements of dimensions down to the smallest detail. Because Jongia conducts this investigation at an early stage, any deviations are still detected and remedied during the production process. This prevents problems afterwards.
Do you have questions about the 3D scan, Jongia’s quality controls or our projects? Please contact us, call +31 (0)58 2139 715 or mail info@jongia.com for more information.
Challenge us to improve your process
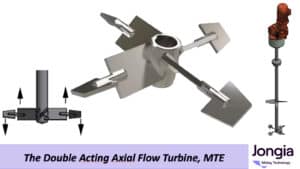
The Double Acting Axial Flow Turbine type AST-MTE mixing element
Operation of an AST-MTE Element Operation of an AST-MTE Element This element can be used in both CW (clockwise) and CCW (counterclockwise) directions. In one case, the inner AST element is downward-pumping with the outer tips pumping upward, and in
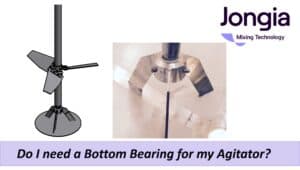
Do I need a Bottom Bearing for my agitator?
Do I need a Bottom Bearing? The installation of a bottom bearing is not mandatory. While it offers certain advantages, there are also drawbacks to consider. It is important to note that the bottom bearing functions more as a displacement
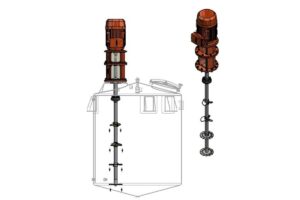
High-Speed Disperser Technology: The Engineering Behind Effective Mixing
A Technical Guide by Jongia Mixing Technology Core Function High-speed dispersers excel at three critical tasks: Fracturing powder agglomerates into fine particles Creating uniform powder distribution throughout liquid mediums Facilitating complete dissolution of soluble materials Operating Principles High-speed dispersers transform