Side Entry Agitators
Light Duty Side Entry Agitators
Types: Magitator (JM), JDRW
Light duty side entry agitators and mixers are the best fit for applications like keeping dairy products homogenous, vegetable oil or juice storage, waste water treatment.
These applications are characterized by:
- Direct driven
- Fluids which are easily mixed or kept homogeneous
- Small tank volumes up to approx. 500 m3
- Low viscous fluids
- Tanks with low pressure
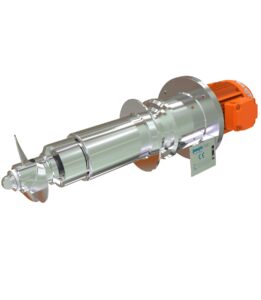
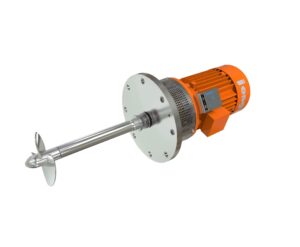
Light Duty Side Entry | |
---|---|
Motor power | 0.25 kW – 15 kW |
Materials | Stainless Steel 304, 316 L, Carbon Steel, Duplex (Super), Hastelloy C4 or C2000, Titanium Grade 2 or 7 |
Coatings | C3, C4, C5 of C5M |
Surface wetted parts | Ground until Ra < 0,4 µm, handpolished till <0,2 μm or electropolished, rubber lined, PTFE or HALAR |
Explosion proof (ATEX) | Ex zone 0, 1 or 2 for gas, 21 or 22 for dust or Non-Ex version |
Accessories | V-belt or gear driven (all brands), all kinds of sealing systems, sterile versions, adapted flanges to vessel |
Medium Duty Side Entry Agitators
Types: JRWM
Medium duty side entry agitators and mixers are suitable for applications like vegetable oil storage, bio digesters, blending (petro)chemical.
Medium duty side entry agitators and mixers have the following characteristics:
- Mixing applications where higher forces are required
- Larger tank volumes
- Fluids with higher viscosity up to approx. 5000 cP
- Tanks with higher pressure (max. 4 bar g)
- Integrated manual leak stop if required
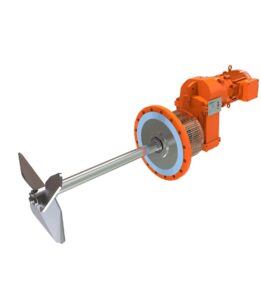
Medium Duty Side Entry | |
---|---|
Motor power | 3 kW - 22 kW |
Materials | Stainless Steel 304, 316 L, Carbon Steel, Duplex (Super), Hastelloy C4 or C2000, Titanium Grade 2 or 7 |
Coatings | C3, C4, C5 of C5M |
Surface wetted parts | Ground until Ra < 0,4 µm, handpolished till <0,2 μm or electropolished, rubber lined, PTFE or HALAR |
Explosion proof (ATEX) | Ex zone 0, 1 or 2 for gas, 21 or 22 for dust or Non-Ex version |
Accessories | V-belt or gear driven (all brands), all kinds of sealing systems, sterile versions, adapted flanges to vessel |
Heavy Duty Side Entry Agitators
Types: RWM
Blending (petro)chemical products, paper & pulp are examples of heavy duty applications where side entry agitators and mixers are selected.
Characteristics for heavy duty agitators and mixers are:
- Mixing applications where extremely high forces are required
- Very large tank volumes (multiple mixers in one tank possible)
- Fluids are highly viscous exceeding even 75.000 cP
- Pressure tanks exceeding even 5 bar
- Temperatures exceeding 250 °C
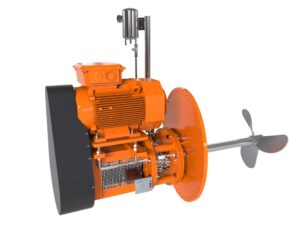
Heavy Duty Side Entry | |
---|---|
Motor power | 11 kW – 55 kW |
Materials | Stainless Steel 304, 316 L, Carbon Steel, Duplex (Super), Hastelloy C4 or C2000, Titanium Grade 2 or 7 |
Coatings | C3, C4, C5 of C5M |
Surface wetted parts | Ground until Ra < 0,4 µm, handpolished till <0,2 μm or electropolished, rubber lined, PTFE or HALAR |
Explosion proof (ATEX) | Ex zone 0, 1 or 2 for gas, 21 or 22 for dust or Non-Ex version |
Accessories | V-belt or gear driven (all brands), all kinds of sealing systems, sterile versions, adapted flanges to vessel |
Frequently Asked Questions
What are side entry agitators used for?
Side entry agitators are utilized in various industries, including food, chemical, pharma, and bio-based applications. They are designed to enhance mixing and homogenization, making them suitable for a wide range of fluids in different tank sizes and viscosities.
What capacities are available for side entry agitators?
We offer side entry agitators in three different capacities: Light Duty, Medium Duty, and Heavy Duty. Each category is tailored for specific applications, ranging from low viscous fluids to highly viscous mixtures, ensuring optimal performance in diverse settings.
What materials are used for constructing side entry agitators?
Our agitators can be made from various materials, including Stainless Steel 304, 316 L, Carbon Steel, Duplex, Hastelloy, and Titanium. This broad selection ensures durability and corrosion resistance, catering to different industrial requirements.
Are side entry agitators available in explosion-proof models?
Yes, we offer explosion-proof versions of our side entry agitators, suitable for Ex zones 0, 1, or 2 for gas and zones 21 or 22 for dust. This feature ensures safety in hazardous environments while maintaining reliable operation.
What types of accessories are available for side entry agitators?
A wide range of accessories is offered including V-belt or gear drives compatible with all brands, numerous sealing systems, sterile versions, and adapted flanges to fit various vessels, enhancing the versatility and functionality of our agitators.
Contact our specialized team for all your questions
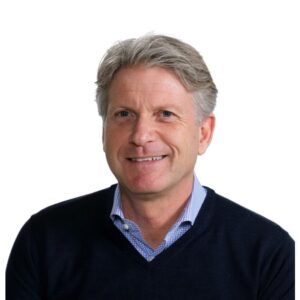
Tom Pruymboom
Sales Director
Area Worldwide
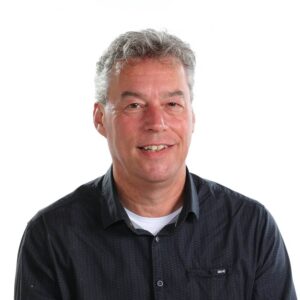
Bart Brouwer
Area Sales Manager
Area Worldwide
Related Articles
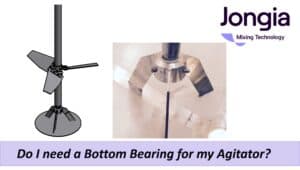
Do I need a Bottom Bearing for my agitator?
Do I need a Bottom Bearing? The installation of a bottom bearing is not mandatory. While it offers certain advantages, there are also drawbacks to consider. It is important to note that the bottom bearing functions more as a displacement
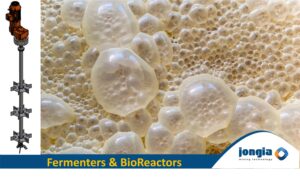
Fermentation & Bioreactor Mixing Process
Bioreactors and Fermenters are culture systems to produce cells or organisms. They are used in various applications, including basic research and development, and the manufacturing of biopharmaceuticals, food and food additives, chemicals, and other products. A broad range of cell types and organisms can be cultivated in bioreactors and Fermenters, including cells (like mammalian cell lines, insect cells, and stem cells), microorganisms (like bacteria, yeasts, and fungi), as well as plant cells and algae. The words “Bioreactor” and “Fermenter” are basically the same thing.
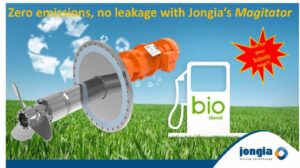
Biodiesel blending with zero leakage!
Fuel blending is a critical component of biodiesel production. A properly blended fuel can increase energy efficiency, reduce emissions and improve performance. However, it can be difficult to achieve consistent fuel quality during blending due to differences in storage tanks,