Top Entry Agitators
Light Duty Top Entry Agitators
Types: FTD, JDR, L
Light duty top entry agitators and mixers are the best fit for applications like cosmetics production, storage of dairy products, ice cream ageing, fragrances and flavourings.
These applications are characterized by:
- Fluids which are easily mixed or kept homogeneous
- Small tank volumes
- Viscosities up to approx. 1000 cP
- Tanks with low pressure (max.10 bar g)
- Temperature -20 °C to 150 °C
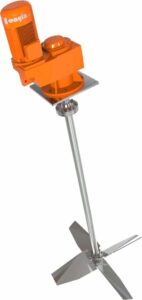

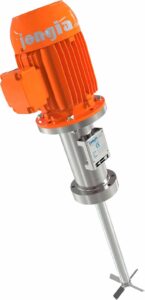
Light Duty Top Entry | |
---|---|
Motor power | 0.25 kW – 15 kW |
Materials | Stainless Steel 304, 316 L, Carbon Steel, Duplex (Super), Hastelloy C4 or C2000, Titanium Grade 2 or 7 |
Coatings | C3, C4, C5 of C5M |
Surface wetted parts | Ground until Ra < 0,4 µm, handpolished till <0,2 μm or electropolished, rubber lined, PTFE or HALAR |
Explosion proof (ATEX) | Ex zone 0, 1 or 2 for gas, 21 or 22 for dust or Non-Ex version |
Accessories | V-belt or gear driven (all brands), all kinds of sealing systems, sterile versions, adapted flanges to vessel |
Medium Duty Top Entry Agitators
Types: LB, NM
Medium Duty top entry agitators and mixers are suitable for applications like yeast fermentation, starch storage, storage and blending of concentrated fruit juices, bitumen and paint production.
Medium duty top entry agitators and mixers have the following characteristics:
- Mixing applications where a higher degree of agitation is required
- Larger tank volumes where a bottom bearing is not desirable
- Viscosities up to approx. 5000 cP
- Pressurized tanks (max. 16 bar g)
- Temperature -20 to 170 °C
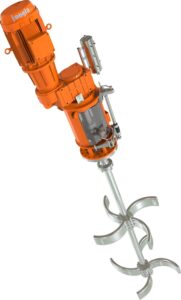
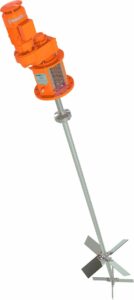
Medium Duty Top Entry | |
---|---|
Motor power | 15 kW - 55 kW |
Materials | Stainless Steel 304, 316 L, Carbon Steel, Duplex (Super), Hastelloy C4 or C2000, Titanium Grade 2 or 7 |
Coatings | C3, C4, C5 of C5M |
Surface wetted parts | Ground until Ra < 0,4 µm, handpolished till <0,2 μm or electropolished, rubber lined, PTFE or HALAR |
Explosion proof (ATEX) | Ex zone 0, 1 or 2 for gas, 21 or 22 for dust or Non-Ex version |
Accessories | Swing out device, lifting device, gear drives (all brands), V-belt or gear driven, all kinds of sealing systems, sterile versions, mobile or stationary versions, adapted flanges to vessel |
Heavy Duty Top Entry Agitators
Types: HD
Examples of heavy duty applications are hydrogenation, bio digesters, chemical reactors, resins.
Characteristics for heavy duty agitators and mixers are:
- Mixing applications where higher forces are required
- Very large tank volumes where a bottom bearing is not applicable
- Highly viscous fluids exceeding even 100.000 cP
- High pressure tanks (exceeding even 100 bar)
- Temperatures exceeding 250 °C
- Shaft supported by double bearing section completely absorbing radial and axial loads
- Flexible coupling between drive and mixer shaft
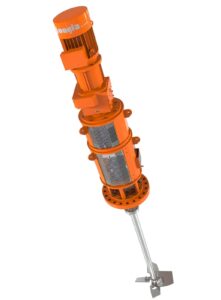
Heavy Duty Top Entry | |
---|---|
Motor power | 15 kW – 200 kW |
Materials | Stainless Steel 304, 316 L, Carbon Steel, Duplex (Super), Hastelloy C4 or C2000, Titanium Grade 2 or 7 |
Coatings | C3, C4, C5 of C5M |
Surface wetted parts | Ground until Ra < 0,4 µm, handpolished till <0,2 μm or electropolished, rubber lined, PTFE or HALAR |
Explosion proof (ATEX) | Ex zone 0, 1 or 2 for gas, 21 or 22 for dust or Non-Ex version |
Accessories | Swing out device, lifting device, gear drives (all brands), V-belt or gear driven, all kinds of sealing systems, sterile versions, mobile or stationary versions, adapted flanges to vessel |
Top Entry Agitators - FAQ
What capacities do your top entry agitators have?
We offer our top entry agitators in three different capacities, catering to the diverse needs of various industries. Whether for light, medium, or heavy duty applications, we ensure the right solution is available for your specific requirements.
What industries can benefit from these agitators?
Our top entry agitators are designed for a range of applications, including food, chemicals, pharmaceuticals, and bio-based processes. We aim to provide optimal mixing solutions tailored to the standards of each industry, ensuring effective results.
What types of materials are used in manufacturing?
We utilize high-quality materials like Stainless Steel 304, 316L, Carbon Steel, Duplex, Hastelloy, and Titanium for our agitators. This ensures durability and performance in various conditions, making them suitable for different applications.
Can I get explosion-proof models?
Yes, our top entry agitators can be designed to be explosion-proof (ATEX compliant). They are suitable for different zones, ensuring safety in environments where explosive gases or dust may be present during operations.
What types of accessories are available for these agitators?
We provide a range of accessories, including swing-out devices, lifting devices, gear drives, and sealing systems. Our agitators can also be customized with sterile versions and adapted flanges to meet specific operational needs.
Contact our specialized team for all your questions
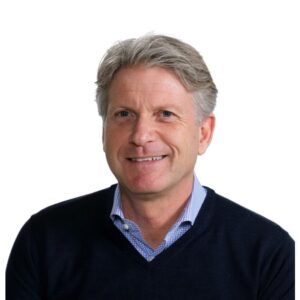
Tom Pruymboom
Sales Director
Area Worldwide
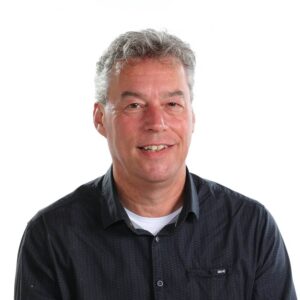
Bart Brouwer
Area Sales Manager
Area Worldwide
Top Entry Agitator Articles
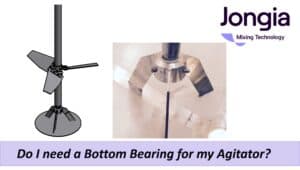
Do I need a Bottom Bearing for my agitator?
Do I need a Bottom Bearing? The installation of a bottom bearing is not mandatory. While it offers certain advantages, there are also drawbacks to consider. It is important to note that the bottom bearing functions more as a displacement
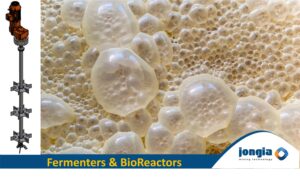
Fermentation & Bioreactor Mixing Process
Bioreactors and Fermenters are culture systems to produce cells or organisms. They are used in various applications, including basic research and development, and the manufacturing of biopharmaceuticals, food and food additives, chemicals, and other products. A broad range of cell types and organisms can be cultivated in bioreactors and Fermenters, including cells (like mammalian cell lines, insect cells, and stem cells), microorganisms (like bacteria, yeasts, and fungi), as well as plant cells and algae. The words “Bioreactor” and “Fermenter” are basically the same thing.
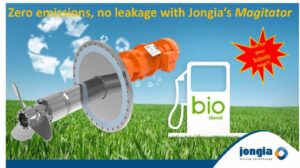
Biodiesel blending with zero leakage!
Fuel blending is a critical component of biodiesel production. A properly blended fuel can increase energy efficiency, reduce emissions and improve performance. However, it can be difficult to achieve consistent fuel quality during blending due to differences in storage tanks,